Zawory EVN
Niebezpieczny GLUTEN – nie wiemy, czy szkodzi, ale z pewnością jest wybuchowy [Sprawdź swój produkt]
GLUTEN – nie wiemy czy szkodzi, ale z pewnością jest wybuchowy…
… podobnie jak cukier, mąka, maltodekstryna, herbata czy setki innych produktów stosowanych w przemyśle spożywczym
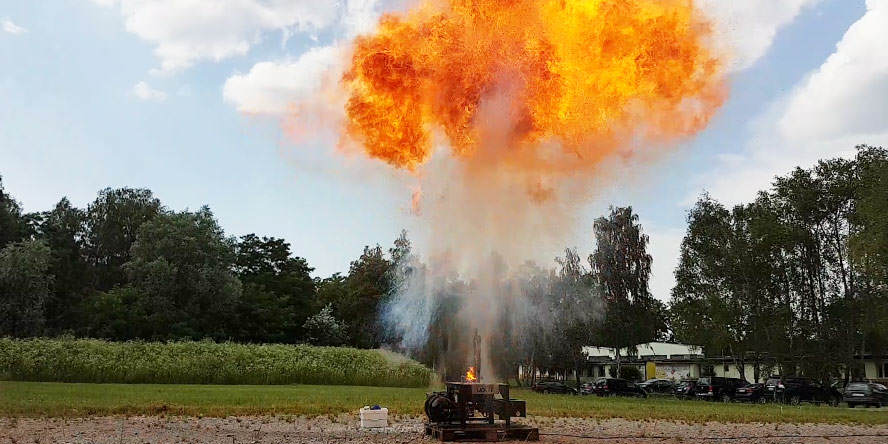
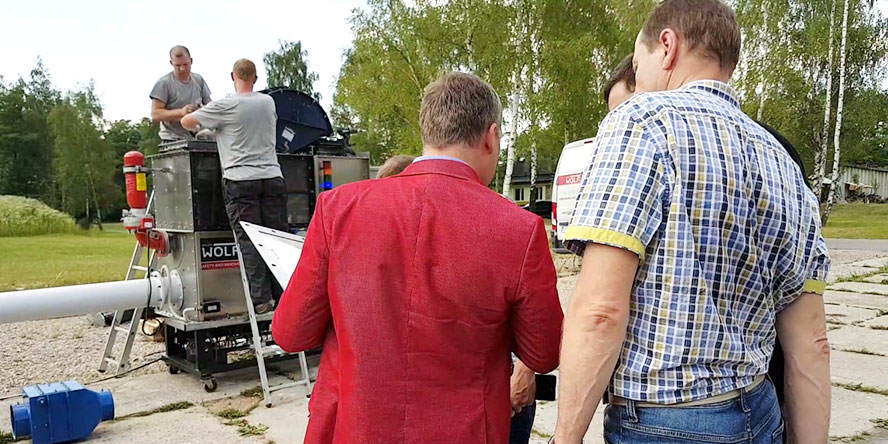
A czy Twój produkt jest wybuchowy?
Posiadamy dostęp do bazy kilkudziesięciu tysięcy produktów, jeśli chcesz dowiedzieć się czy Twój produkt jest wybuchowy kliknij w poniższy guzik.
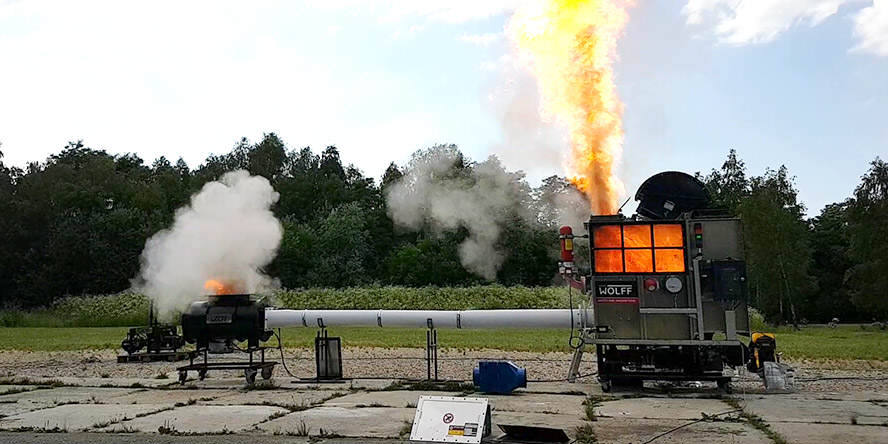
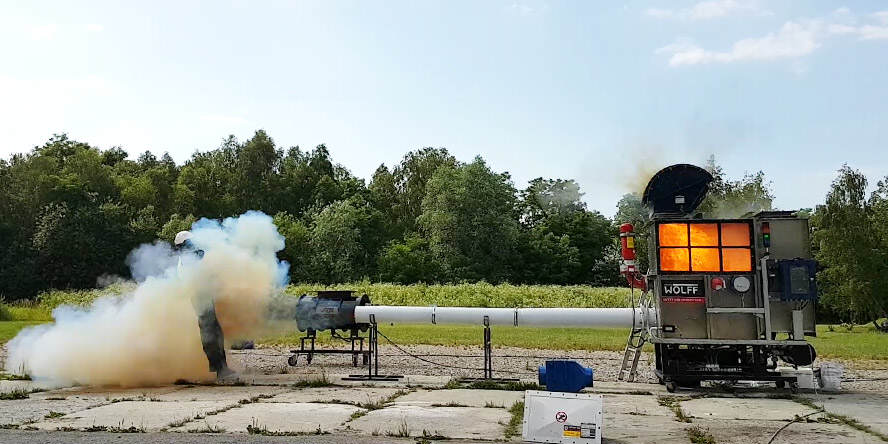


Dużo ostatnio słyszy się o glutenie i jego szkodliwym wpływie na zdrowie. My co prawda nie oceniamy jego negatywnego działania na organizm, ale wiemy jedno – gluten jest wybuchowy i w przemyśle stwarza poważne zagrożenie – podobnie jak setki innych produktów, w tym m.in.: cukier, mąka, maltodekstryna, herbata czy przyprawy.
Wiedzą o tym również nasi goście z młynowni glutenu na Litwie, którzy niedawno odbyli w siedzibie naszej firmy szkolenie z zakresu bezpieczeństwa wybuchowego w przemyśle.
O tym jak niebezpieczny jest gluten inżynierowie z młynowni przekonali się podczas pokazu wybuchów, który był uzupełnieniem merytorycznego szkolenia. W pokazie wykorzystano dostarczony przez naszych gości produkt. W filtrze odpylającym zainicjowano wybuch zaledwie kilkuset gramów glutenu i zaprezentowano działanie poszczególnych zabezpieczeń przeciwwybuchowych tj. odpowietrzania, izolacji i tłumienia wybuchu. Ponadto zademonstrowano wybuch glutenu na otwartej przestrzeni. Okazało się, że zapłon niewielkich ilości pyłu glutenu może doprowadzić do silnej eksplozji. Jakie zagrożenie stwarza gluten w warunkach przemysłowych? Z pewnością ogromne!
Parametry wybuchowości glutenu
Aby uniknąć niebezpiecznych konsekwencji wybuchu należy stosować odpowiednie systemy ochronne. Podstawą do prawidłowego określenia skali zagrożenia i odpowiedniego doboru niezbędnych zabezpieczeń jest znajomość parametrów wybuchowości danej substancji. Należy pamiętać, że na ogół dane zaczerpnięte z literatury nie są jednoznaczne, dlatego zawsze zalecamy przeprowadzenie badań znajdującego się na zakładzie produktu przez jednostkę notyfikowaną. Poznaj zakresy parametrów wybuchowości zbadanych dla różnych próbek czterech typowych produktów.
Produkt | DGW [gm/m3] | Kst [bar x m/s] | Pmax [bar] | MEZ [mJ] |
---|---|---|---|---|
Gluten | 30-200 | 64-110 | 7,7-8,7 | 0,01->10 |
Cukier | 30-200 | 30-200 | 30-200 | 30-200 |
Maltodekstryna | 30-200 | 30-200 | 30-200 | 30-200 |
Herbata | 30-200 | 30-200 | 30-200 | 30-200 |
Parametry wybuchowości – co oznaczają?
W powyższej tabeli prezentujemy parametry wybuchowości dla czterech produktów powszechnie stosowanych w przemyśle spożywczym. Problem zagrożenia wybuchem dotyka jednak znacznie większej ilości substancji. Aby sprawdzić czy produkty stosowane na Twoim zakładzie produkcyjnym stwarzają ryzyko wybuchu, a jeśli tak to jakie mogą być konsekwencje takiego zdarzenia, wypełnij i prześlij poniższy formularz, w odpowiedzi otrzymasz niezbędne informacje.
Aby prawidłowo rozumieć parametry wybuchowe pyłów poniżej prezentujemy ich definicje z praktycznym komentarzem.
Stężenie palnego gazu, pary, pyłu lub włókien w powietrzu, poniżej którego nie utworzy się atmosfera wybuchowa.
Maksymalna wartość szybkości narastania ciśnienia wybuchu (dp/dt)max, zmierzona podczas wybuchu określonej atmosfery wybuchowej w zamkniętym zbiorniku o objętości 1 m3, w określonych warunkach badania.
Wskaźnik Kmax (Kst) jest podstawą klasyfikacji palnych pyłów. Podział na klasy wybuchowości przedstawiamy poniżej:
- 0 < Kst < 200 | Klasa wybuchowości St 1 | Produkt wybuchowy
- 200 < Kst < 300 | Klasa wybuchowości St 2 | Produkt silnie wybuchowy
- Kst < 300 | Klasa wybuchowości St 3 | Produkt bardzo silnie wybuchowy
Maksymalne ciśnienie występujące w zamkniętym naczyniu podczas wybuchu atmosfery wybuchowej, oznaczone w określonych warunkach badania.
Najmniejsza energia, która jest wystarczająca do spowodowania zapłonu najłatwiej zapalnej atmosfery wybuchowej w określonych warunkach badania.
Wybuch pyłu aluminium
Wybuch pyłu aluminium
Tak, jak obiecałem wczoraj, poniżej publikuję krótki filmik z dzisiejszego pokazu wybuchu przestrzennego. Do testu użyliśmy ok. 200 gramów sproszkowanego aluminium. Kilkanaście sekund wystarczyło, by przekonać się jak ogromna siła drzemie w tak pozornie niewielkiej ilości produktu! Uczestnicy pokazu byli pod wrażeniem – nie dało się nie odczuć siły fali uderzeniowej!
Bazując na swoim wieloletnim doświadczeniu zauważamy, że znaczącym problemem wśród przedsiębiorców i pracowników zakładów przemysłowych jest brak odpowiedniej wiedzy na temat produktów stanowiących zagrożenie. Dla wielu osób nie jest oczywistym, że nawet powszechnie stosowane substancje takie jak mąka, cukier, pył drzewny czy pył węglowy mogą ulec zapłonowi. To dlatego realizujemy pokazy kontrolowanych wybuchów, które nie tylko podnoszą świadomość skali ryzyka, ale również pokazują rozwiązania techniczne, które mogą w znaczący sposób wpłynąć na przebieg wybuchu i zniwelować jego skutki do minimalnego poziomu.
FIRMA Z LUDZKĄ TWARZĄ
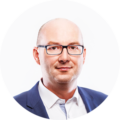
Nie chcemy być kolejną anonimową firmą…
Nie chcemy być kolejną anonimową firmą, opartą na powierzchownych relacjach typu fast-food. W biznesie szukamy czegoś więcej – zaufania, partnerstwa i ludzkiej twarzy. To na tych fundamentach chcemy budować GRUPĘ WOLFF. Nie jest to łatwe w świecie zdominowanym przez korporacyjny, chłodny styl prowadzenia biznesu. Zapewniam jednak, że będziemy starać się podążać własną drogą. Drogą biznesu z ludzką twarzą.
Dlatego, poprzez kanał na portalu LinkedIn oddaję się do waszej dyspozycji. Każdy z Was – klientów, partnerów, pracowników, a także potencjalnych pracowników czy klientów może zadać mi pytanie. Gwarantuje, że odpowiem na każde z nich.
Ze swojej strony będą chciał pokazywać Wam firmę od kuchni, udostępniać ciekawostki z branży, ciekawe konkursy oraz własne przemyślenia, czyli wszystko to co może Was zainteresować. Dołącz do mnie i bądźmy w kontakcie.
Z dumą prezentuję wyniki ankiety nt. konferencji HAZEX
Z dumą prezentuję wyniki ankiety nt. konferencji HAZEX
Z wielką dumą prezentuję wyniki ankiety oceniającej naszą konferencję HAZEX nt. bezpieczeństwa wybuchowego i procesowego w przemyśle (www.hazex.eu/wydarzenia/konferencja-hazex):
– 96% uczestników oceniło poziom merytoryczny konferencji jako wysoki lub b. wysoki
– 96% uczestników jest zadowolonych lub b. zadowolonych z udziału – 100% uczestników uznało, że organizacja konferencji była na wysokim lub bardzo wysokim poziomie
– 92% uczestników podczas wspólnego bankietu bawiło się dobrze lub b. dobrze
Szczerzę dziękuję wszystkim osobom zaangażowanym w organizację konferencji HAZEX nt. bezpieczeństwa wybuchowego i procesowego w przemyśle. Z pewnością była to nasza najlepsza z pięciu dotychczasowych edycji. Widzę ciągły progres, dlatego jestem przekonany, że kolejna będzie jeszcze lepsza.
FIRMA Z LUDZKĄ TWARZĄ
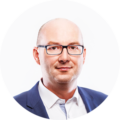
Nie chcemy być kolejną anonimową firmą…
Nie chcemy być kolejną anonimową firmą, opartą na powierzchownych relacjach typu fast-food. W biznesie szukamy czegoś więcej – zaufania, partnerstwa i ludzkiej twarzy. To na tych fundamentach chcemy budować GRUPĘ WOLFF. Nie jest to łatwe w świecie zdominowanym przez korporacyjny, chłodny styl prowadzenia biznesu. Zapewniam jednak, że będziemy starać się podążać własną drogą. Drogą biznesu z ludzką twarzą.
Dlatego, poprzez kanał na portalu LinkedIn oddaję się do waszej dyspozycji. Każdy z Was – klientów, partnerów, pracowników, a także potencjalnych pracowników czy klientów może zadać mi pytanie. Gwarantuje, że odpowiem na każde z nich.
Ze swojej strony będą chciał pokazywać Wam firmę od kuchni, udostępniać ciekawostki z branży, ciekawe konkursy oraz własne przemyślenia, czyli wszystko to co może Was zainteresować. Dołącz do mnie i bądźmy w kontakcie.
Za nami V edycja konferencji HAZEX – zobacz jak zgłębialiśmy tajniki bezpieczeństwa wybuchowego i procesowego w przemyśle
Słowem wstępu
Pięć lat temu zrodził się pomysł, by stworzyć konferencję, która byłaby spotkaniem ekspertów mogących wymienić się informacjami technicznymi na tle zmieniających się przepisów w zakresie bezpieczeństwa w przemyśle. Wiedza ta byłaby niezbędna dla użytkowników, którzy na co dzień planują i wykonują prace na instalacjach przemysłowych. Konferencja HAZEX powstała jako odpowiedź na zapotrzebowanie rynku i moje osobiste obserwacje. W imieniu całej GRUPY WOLFF dziękuję wszystkim obecnym za udział w tegorocznej, już piątej edycji konferencji i zapraszam na relację z wydarzenia. W tym miejscu chciałbym również zaprosić na przyszłoroczną edycję, która odbędzie się w IV kw. 2018 roku. Będzie ona skierowana ku zagadnieniom bezpieczeństwa wybuchowego i procesowego w zakładach stosujących niebezpieczne gazy i ciecze (więcej>>).

Bartosz Wolff
Prezes GRUPY WOLFF
W dniach 26-27 października br. odbyła się V edycja Międzynarodowej Konferencji HAZEX, która zgromadziła niespełna 170 osób z branży energetycznej, drzewnej, spożywczej, chemicznej, farmaceutycznej i pokrewnych. Jej tematyka skupiała się głównie na zagrożeniach wynikających z obecności w procesach produkcyjnych palnych, a tym samych wybuchowych pyłów.
Kto nas odwiedził
Grono uczestników wydarzenia z roku na rok się powiększa. W tegorocznym spotkaniu odwiedzili nas przedstawiciele kadry kierowniczej i inżynierskiej działów technicznych, działów utrzymania ruchu, BHP i ppoż., technolodzy i projektanci, a także przedstawiciele firm ubezpieczeniowych. Wśród gości znaleźli się delegaci takich firm jak ABB, Whirlpool, PGE, PZU, Carlsberg, LOTOS, FLUOR, 3M, Pfeifer & Langen, Amec Foster Wheeler Energia, Benda-Lutz, ADAMED, HASCO-LEK, Hestia Loss Control, Texas A&M University w Katarze oraz wielu innych.
Staramy się, by każda kolejna konferencja była lepsza od poprzedniej, nie tylko pod kątem organizacyjnym, ale przede wszystkim merytorycznym. Prelegentami tegorocznego wydarzenia byli zarówno polscy jak i zagraniczni eksperci i praktycy związani od lat z branżą bezpieczeństwa wybuchowego i procesowego. Dwudniowe spotkanie naszpikowane było merytorycznymi wykładami i upłynęło pod znakiem rozmów związanych z podstawami prawnymi w zakresie bezpieczeństwa produkcji, przewidywaniem skutków potencjalnego wybuchu oraz rozwiązaniami technicznymi stosowanymi w strefach zagrożenia wybuchem, czyli tym, z czym uczestnicy na co dzień się spotykają.
Wydarzenie była ogromnym sukcesem, o czym świadczą wyniki anonimowej ankiety przeprowadzonej wśród uczestników po zakończeniu konferencji.
Aż 96% uczestników oceniło poziom merytoryczny konferencji jako wysoki lub bardzo wysoki i jest zadowolonych lub bardzo zadowolonych z udziału.
Prelekcje
Po słowach wstępu Prezesa GRUPY WOLFF konferencję rozpoczął szereg wykładów. Inne podejście do oceny ryzyka wybuchu, wynikające z lat doświadczeń, przedstawił dr hab. inż. Andrzej Wolff. W prelekcji poruszony został aktualny stan prawny dotyczący wspomnianej oceny ryzyka wybuchu i ograniczeń z niego wynikających, jak również zapisy odnoszące się do zagrożeń przeniesienia się wybuchu z aparatu procesowego na sąsiednie urządzenia. Wykładowca zaznaczył, iż podejście do pewnych kwestii związanych z analizą i oceną ryzyka wybuchu nie jest wystarczające, ponieważ nie bierze ono pod uwagę szeregu czynników procesowych, omówionych podczas prelekcji. Nowe podejście do oceny ryzyka wybuchu wpłynęłoby na rzetelną ocenę możliwych zagrożeń, lepszą ochronę zdrowia i życia ludzkiego, a także bardziej korzystną ochronę środowiska i miejsc prac – mówił dr. hab. inż. Andrzej Wolff. Prelekcja spotkała się z dużym zainteresowaniem, czego potwierdzeniem była duża ilość zadawanych przez gości pytań.
Zagadnienia związane z dyrektywą ATEX user przybliżył uczestnikom dr inż. Michał Górny z Urzędu Dozoru Technicznego. W prezentacji ujęto m.in. cel dyrektywy i korzyści dla użytkownika jakie z niej wynikają, a także omówiono strukturę Dokumentu Zabezpieczenia Przed Wybuchem. Podobnie jak w przypadku pierwszego wykładu i ten spotkał się z zalewem pytań związanych z dyrektywą i jej implementacją. Ostatnia z prezentacji z pierwszego bloku tematycznego była prowadzona przez pana Pawła Wąsowicza, praktyka w dziedzinie bezpieczeństwa procesowego. Dotyczyła ona analizy i oceny ryzyka wybuchu na instalacjach przemysłowych na podstawie scenariuszy wybuchu. Świadomość pracowników jest kluczem zapewnienia bezpieczeństwa – mówił podczas swojego wykładu Mariusz Balicki, specjalista od wielu lat związany z techniką przeciwwybuchową. Jego prelekcja uświadomiła uczestnikom jaki wpływ na bezpieczeństwo produkcji mają kompetencje pracowników oraz ich zakres. Następnie Grzegorz Ogrodnik ze Szkoły Głównej Służby wyjaśnił gościom różnicę między strefą a pomieszczeniem zagrożonym wybuchem ze względu na ich koncepcje, które bazują na różnych założeniach.
Świadomość pracowników jest kluczem zapewnienia bezpieczeństwa.
(Mariusz Balicki, GRUPA WOLFF)
Tematem kolejnego wykładu było „Spojrzenie na bezpieczeństwo wybuchowe w kontekście analizy ryzyka dla potrzeb ubezpieczeń”. Ryzyko pojawia się we wszystkich dziedzinach życia ludzkiego. Jest też nieodłącznym elementem procesów przemysłowych – mówił Rafał Żuchowski z PZU LAB S.A., który na co dzień zajmuje się analizą i zarządzaniem ryzykiem obiektów przemysłowych. Bardzo ciekawą prelekcją Camille Azzi (GEXCON) przybliżył słuchaczom informacje nt. nowoczesnych narzędzi, które umożliwiają przewidywanie skutków wybuchu. Techniczne aspekty związane z zabezpieczeniami przeciwwybuchowymi podnośników kubełkowych przedstawił Zbigniew Wolff, który od wielu lat zajmuje się zabezpieczeniem instalacji i zakładów przemysłowych przed skutkami niekontrolowanego wybuchu. Wykład obejmował prawidłowe podejście do zabezpieczenia podnośników kubełkowych oraz ukazanie przykładowych skutków braku lub nieprawidłowego zabezpieczenia układów transportu pneumatycznego. Jako ostatni zabrał głos Ulrich Lamerz z IEP Technologies, który omówił zastosowanie systemów detekcji na przykładzie instalacji odpylania. Pomimo bariery językowej wykład spotkał się z dużym zainteresowaniem. Po ostatniej tego dnia serii pytań nastąpiła krótka przerwa, po której uczestnicy konferencji zostali przewiezieni na pokaz wybuchów.
Ryzyko pojawia się we wszystkich dziedzinach życia ludzkiego. Jest też nieodłącznym elementem procesów przemysłowych.
(Rafał Żuchowski, PZU LAB S.A.)
20 lat w branży zabezpieczeń przemysłowych i detekcji pożaru to spore doświadczenie. Drugi dzień wykładów rozpoczął Arkadiusz Waligóra (CREATIO), który przeprowadził słuchaczy przez aspekty techniczne przenośników paliw, koncepcje, przepisy prawne aż po ich zastosowania, a wszystko w odniesieniu do detekcji pożaru. Kolejna z prezentacji miała na celu przedstawienie powiązania aspektów związanych z ogólnie pojętym bezpieczeństwem procesowym z wymaganiami zawartymi w przepisach prawa i innych regulacjach normatywnych na etapie projektu koncepcyjnego, jak również związku bezpieczeństwa procesowego i wybuchowego z wymaganiami ochrony środowiska na etapie projektowanych inwestycji. Zagadnienia te poruszył Wacław Smardzewski (GRUPA WOLFF), projektant instalacji technologicznych z wieloletnim doświadczeniem, zajmujący się kwestiami bezpieczeństwa wybuchowego i procesowego. Kolejny wykład należał do Adama Rybskiego (PROCOM SYSTEM), który wprowadził uczestników w nowy wymiar zarządzania produkcją w zakładach z podwyższonym ryzykiem eksplozji i opowiedział o możliwościach systemu ExPlant, który został stworzony we współpracy z GRUPĄ WOLFF. Następnie o systemach zasilania i sterowania oświetleniem w pyłowych strefach zagrożenia wybuchem opowiedział Maciej Freza z GRUPY WOLFF, specjalista w zakresie opraw i systemów oświetlenia awaryjnego. Zaraz po nim na scenę wszedł Łukasz Klimek, od ponad kilkunastu lat związany z branżą elektrotechniczną ze szczególnym uwzględnieniem systemów oświetleniowych. Jego wykład był kontynuacją wcześniejszej prelekcji i dotyczył istotnych parametrów opraw oświetlenia w technologii LED dla stref zagrożenia wybuchem i innych aplikacji przemysłowych.
Kolejną, równie ciekawą prelekcję wygłosił Adama Galewski z firmy Hensel, który poruszył temat bezpieczeństwa personelu w kontekście wykonania materiałowego systemów bezpieczeństwa. Czy drony gwarantują bezpieczeństwo? Kolejne wystąpienie to duet Roberta Walenia i Krzysztofa Śmierciaka (UAVS), którzy opowiedzieli o możliwościach zabezpieczania terenu zewnętrznego obiektów przemysłowych przed ingerencją osób trzecich z wykorzystaniem systemów bezpieczeństwa oraz obiektów latających. Na wstępie prelegenci zapoznali uczestników z normami i przepisami dotyczącymi wykorzystania bezzałogowych statków powietrznych oraz systemów wykrywających i neutralizujących drony. Następnie poruszone zostały kwestie integracji systemów bezpieczeństwa. Bez wątpienia interesujący wykład wygłosił Piotr Przybysz (Hestia Loss Control), który przedstawił zgromadzonym jak na kwestie zagrożenia wybuchem zapatrują się ubezpieczyciele. Ryzyko jest funkcją prawdopodobieństwa wystąpienia zdarzenia i wielkości szkody – mówił. Ostatnia prelekcja należała do Mariusza Balickiego, który mówił o typach ochrony przeciwwybuchowej urządzeń elektrycznych. Prelegent wskazał na zasady doboru urządzeń do stref zagrożonych wybuchem i konsekwencje wyboru poszczególnych typów ochrony związane z ich montażem, przeglądami, remontami.
Ryzyko jest funkcją prawdopodobieństwa wystąpienia zdarzenia i wielkości szkody.
(Piotr Przybysz, Hestia Loss Control)
Po każdym z wygłaszanych w ciągu dwóch dni konferencji wykładów uczestnicy mogli zadawać nurtujące ich pytania. Czynny udział nagradzany był hazexami – banknotami, które jak się później okazało, były bardzo cenne…
Wisienka na torcie, czyli pokaz wybuchów na żywo
Nasze wieloletnie doświadczenie pokazuje, że istotnym problemem wśród przedsiębiorców i pracowników zakładów przemysłowych jest brak odpowiedniej wiedzy na temat produktów stanowiących zagrożenie. Dla wielu osób nie jest oczywistym, że powszechne substancje takie jak mąka, cukier, pył drzewny czy pył węglowy mogą ulec zapłonowi. To dlatego oprócz merytorycznych wykładów w ramach naszych konferencji uczestnicy biorą udział w pokazie kontrolowanych wybuchów, który nie tylko podnosi świadomość skali ryzyka, ale również pokazuje rozwiązania techniczne, które mogą w znaczący sposób wpłynąć na przebieg wybuchu i zniwelować jego skutki do minimalnego poziomu.
W ramach konferencji HAZEX uczestnicy zostali przewiezieni na pobliski poligon wojskowy. To właśnie tam, zanim zapadł zmrok, odbył się półtoragodzinny pokaz wybuchów, który był „wisienką na torcie”. Obejmował on wybuchy pyłu cukru w filtrze pokazowym wraz z zastosowaniem poszczególnych systemów przeciwwybuchowych (tłumienia, odciążania i odsprzęgania wybuchu), a także demonstracyjne wybuchy przestrzenne pyłu węgla oraz glutenu. Zdajemy sobie sprawę, że żadne zdjęcia czy filmy nie oddadzą w pełni siły zjawiska. Poprzez oglądanie fotografii nie da się przecież odczuć ciepła i fali ciśnienia… musicie nam więc zaufać, że udział w takim pokazie robi wrażenie.
Nie samą wiedzą żyje inżynier
Jak się okazało, pokaz wybuchów nie był jedyną z atrakcji. Po powrocie z poligonu goście zostali zaproszeni na uroczystą kolację, którą niewątpliwie urozmaicił występ dziesięcioosobowego zespołu Kraków Street Band. Panowie urzekli wszystkich swoją muzyką bigbandową i bluegrassową. Ale to nie wszystko… Impreza miała swój motyw przewodni – tego wieczoru każdy mógł przez chwilę poczuć się jak Al Capone popijający whisky w jednym z wielkich, rozświetlonych kasyn. Przy wejściu na kolację mężczyźni zostali obdarowani kapeluszami, kobiety zarzuciły na szyję szale boa i wszyscy przenieśli się do okresu prohibicji. Na każdego czekał plik 12 banknotów o łącznej wartości 1200 hazex’ów. Jak się domyślacie, ci, którzy czynnie zadawali pytania po każdym z wykładów, mieli ich jeszcze więcej. Posłużyły one gościom do zakupu alkoholu z kontrabandy, drogocennych fantów – w tym nieocenionego WOLFF PREMIUM BEER – a co najważniejsze – do gry w kasynie, co pozwalało jeszcze bardziej zwiększyć swoje zaplecze finansowe. Impreza czasami prohibicji. Kolacja „gangsterów” trwała do późnych godzin wieczornych i była wypełniona dobrą zabawą, pysznym jedzeniem i świetną muzyką.
Masz pytania dotyczące kolejnej edycji konferencji? Skontaktuj się z nami
+48 12 2018 100
Zobacz całą fotogalerię
Ropa naftowa
„Wszystko jest trucizną i nic nią nie jest” – pozytywne oblicze amoniaku
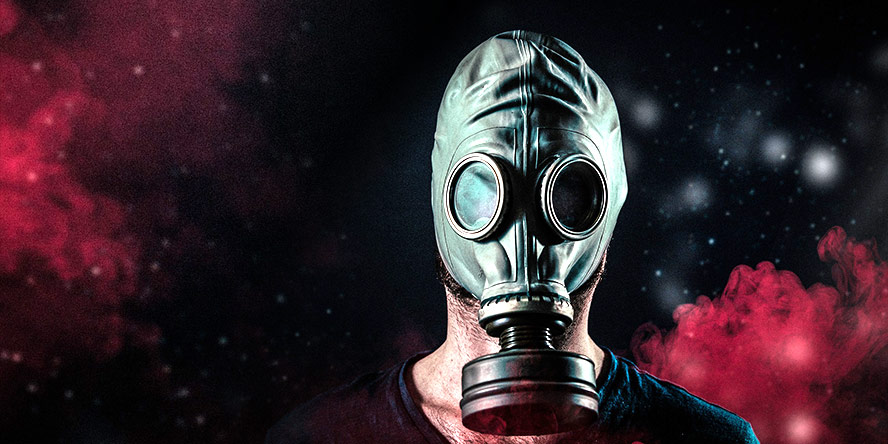
Amoniak powszechnie stosowany w przemyśle, jak i gospodarstwie domowym jest jednym z pierwszych znanych i wyodrębnionych związków chemicznych. Jest on niezwykle pożyteczny, ale jest również śmiertelnie groźny. Przebywając w otoczeniu, gdzie unoszą się opary amoniaku, ryzykujemy zdrowiem, czasem też życiem. Możemy doznać trwałego uszczerbku na zdrowiu, a nawet umrzeć. W tym artykule skupimy się jednak na pozytywnej stronie współżycia człowieka z amoniakiem.
Otrzymywanie amoniaku
Pierwszy opisany związek amoniaku, tzw. salmiak (związek chemiczny chlorek amonu), otrzymany został ok. 332 roku p.n.e. z odchodów wielbłądów w pobliżu świątyni Amona, w oazie Siwa na terenie dzisiejszego Egiptu. Stąd pochodzi nazwa „amoniak”, która jest używana w różnych formach w większości języków świata. Chlorek amonu był też znany przez średniowiecznych alchemików – wzmiankował o nim Albert Wielki na początku XII wieku. Skład amoniaku został ustalony ostatecznie przez Claude’a Luisa Bertholleta w XVIII wieku. W naturze amoniak powstaje jako produkt rozkładu biologicznego substancji organicznych m.in. w nawozie z hodowli zwierząt.
Przed wynalezieniem metod syntetycznych do przemysłowego otrzymywania amoniaku uzyskiwano go w reakcji hydrolizy cyjamidu wapnia, w suchej destylacji drewna, niektórych roślinach i produktach zwierzęcych oraz w redukcji kwasu azotawego i jego soli wodorem.
W chwili obecnej najczęściej stosuje się metody:
- syntezy Habera/Boscha polegającej na bezpośredniej syntezie azotu i wodoru w obecności katalizatora w temperaturze ok. 700ºC i pod ciśnieniem 20 MPa,
- syntezy azotu i wodoru w procesie parowego reformingu gazu ziemnego i lekkich węglowodorów w temperaturze 100ºC i ciśnieniu 25 MPa,
- syntezy azotu i wodoru w procesie półspalania powietrzno-tlenowego lub tlenowego ciężkich olejów opałowych w temperaturze 100ºC i ciśnieniu 25 MPa.
Światowa wielkość produkcji amoniaku osiągnęła w 2015 roku 240,2 mln Mg z perspektywą wzrostu w 2018 roku do 249,8 mln Mg.
Amoniak i jego pochodne są podstawowym surowcem stosowanym we wszystkich dziedzinach przemysłu, m.in. :
- w produkcji nawozów,
- w produkcji włókien syntetycznych,
- w produkcji tworzyw sztucznych i chemikaliów,
- w produkcji materiałów wybuchowych,
- w metalurgii,
- w chłodnictwie przemysłowym,
- jako substrat w procesach chemicznych i petrochemicznych,
- w instalacjach odsiarczania spalin (woda amoniakalna).
Opisane powyżej zastosowania amoniaku są powszechnie znane i przedstawione w literaturze przedmiotu. Można go również z zaskakująco dużym powodzeniem stosować w gospodarstwie domowym, o ile oczywiście przezwyciężymy niechęć do jego zapachu.
Oto kilka przykładowych „domowych” i nietypowych zastosowań amoniaku:
- Mycie okien – smugi powstałe w trakcie mycia okien często powodują, że trzeba umyć szyby jeszcze raz. Można tego uniknąć, jeśli zamiast zwykłego płynu do mycia szyb wykorzysta się roztwór 3 szklanek wody z 1 szklanką amoniaku. Nie tylko okna będą nieskazitelnie czyste, ale nie pojawią się na nich żadne smugi ani zacieki. Wystarczy zanurzyć ścierkę w roztworze i myć.
- Likwidacja moli – pojawiające się znienacka mole potrafią skutecznie utrudnić życie. Żeby szybko się ich pozbyć, warto użyć amoniaku. Należy roztworem z 1/2 szklanki amoniaku oraz 1 litra wody umyć wszystkie szafy, szafki, szuflady kuchenne, w których mogłyby zagnieździć się szkodniki. Można również wyczyścić szafy z ubraniami, jednak wówczas należy pamiętać o wywietrzeniu ich po umyciu, aby zapach amoniaku nie wniknął w odzież.
- Czyszczenie kryształów – kryształowe kieliszki wymagają specjalnego czyszczenia, by nie matowieć i nie wyglądać na zaniedbane. Aby zawsze stanowiły miły dla oka element zastawy, można przecierać je miękką szmatką zamoczoną w roztworze z 2 szklanek wody oraz 5 kropel amoniaku. Amoniak przywróci im odpowiedni blask, jednak trzeba pamiętać, by po przetarciu kryształów roztworem opłukać je w zimnej wodzie oraz dokładnie wytrzeć.
- Likwidacja zapachu – po remoncie w odmalowanych pomieszczeniach długo unosi się zapach gładzi, gipsu albo farby. Szybko i skutecznie można pozbyć się niechcianej woni, wystarczy ustawić w pokoju, 3–4 niewielkie miseczki z amoniakiem. Już po 3 dniach zapach farby zostanie wchłonięty przez amoniak.
- Usuwanie plam – plama to problem, zwłaszcza na ulubionym ubraniu lub nowej rzeczy. Szczególnie uciążliwe są tłuste plamy, jednak amoniak może poradzić sobie również z nimi. Wystarczy przygotować roztwór z amoniaku, wody i płynu do mycia naczyń. Należy pamiętać, aby proporcje roztworu były równe, np. 1 : 1 : 1, a sam specyfik umieszczony w butelce z dozownikiem. Amoniak z płynem nanosi się na plamę i pozostawia na 5 minut. Po tym czasie trzeba dokładnie wypłukać ubrudzone miejsce. Zabrudzenie powinno być już niewidoczne.
Jak wynika z przedstawionego materiału, amoniak jest związkiem chemicznym, od którego nasze życie jest w olbrzymim stopniu uzależnione. Poza pozytywnymi skutkami niesie jednak szereg zagrożeń, których jeśli nie da się całkowicie wyeliminować, to w maksymalnym stopniu trzeba je ograniczyć.
Już w XVI wieku niemiecki lekarz i alchemik Paracelsus powiedział: „Wszystko jest trucizną i nic nią nie jest. Dawka i czas ekspozycji decydują tylko, czy coś jest, czy nie jest trucizną”. Teza ta jak zawsze pozostaje aktualna.
Czwartki z bezpieczeństwem, czyli zupełnie nowa formuła szkoleń
Czwartki z bezpieczeństwem
Reprezentujesz kadrę kierowniczą lub inżynierską działu technicznego w swojej firmie? Pracujesz w dziale utrzymania ruchu, BHP, ppoż., a może jesteś technologiem lub projektantem? Chcesz zgłębić swoją wiedzę w konkretnym temacie z zakresu bezpieczeństwa wybuchowego i procesowego? Mamy dla Ciebie doskonałą propozycję – zarezerwuj dla siebie jeden dzień tygodnia i weź udział w „czwartku z bezpieczeństwem”.
Harmonogram spotkań znajdziesz poniżej.


Na czym to polega?
Czwartki z bezpieczeństwem to zupełnie nowy format szkoleń, który właśnie wdrażamy. Charakteryzują się one stosunkowo krótką częścią wykładową (około 2-4 godzin), która skupia się na wąskiej tematyce oraz wyjątkowo długą częścią dyskusyjną. W ten sposób jesteśmy w stanie zgłębić problem, a co najważniejsze odpowiedzieć na konkretne pytania uczestników. Zwieńczeniem wykładu i dyskusji jest wspólna kolacja. Spotkania odbywają się raz w miesiącu, dzień po pełnowymiarowych szkoleniach z zakresu ATEX, o których więcej informacji znajdziesz tutaj>>.
Dlaczego warto?
Wąska tematyka spotkania umożliwiająca szczegółowe omówienie konkretnego problemu
Luźna atmosfera
sprzyjająca swobodnej dyskusji
i zadawaniu nurtujących pytań
Miejsce wymiany spostrzeżeń
i doświadczeń, również z kolegami
„po fachu”
Możliwość korzystania z wiedzy specjalistycznej przedstawicieli różnych branż przemysłowych
KIEDY
Czwartki z bezpieczeństwem odbywają się raz w miesiącu. Poniżej znajdziesz harmonogram najbliższych spotkań i ich tematykę. W razie zainteresowania zachęcamy do udziału w pełnowymiarowych szkoleniach z zakresu ATEX, które odbywają się dzień przed czwartkiem z bezpieczeństwem (więcej>>).
GDZIE
Na chwilę obecną czwartki z bezpieczeństwem odbywają się w Krakowie oraz Poznaniu. Po szkoleniu, w pobliskiej restauracji odbywa się wspólna kolacja, której koszt pokrywa organizator. Dojazd do restauracji pozostaje w gestii uczestników.

Harmonogram spotkań
08.02.2017 | Kraków, Balice
Separatory, przesiewacze, podajniki celkowe – poprawny dobór i eksploatacja

08.03.2017 | Kraków, Balice
Prawidłowa eksploatacja systemów odciążania i tłumienia wybuchów

22.03.2018 | Poznań
Bezpieczeństwo produkcji w strefach gazowych – systemy detekcji gazów, przerywacze płomienia

05.04.2018 | Kraków, Balice
Oświetlenie awaryjne i ewakuacyjne oraz osprzęt elektrotechniczny w wykonaniu Ex

10.05.2018 | Kraków, Balice
System zarządzania bezpieczeństwem, produkcją i eksploatacją urządzeń

07.06.2018 | Kraków, Balice
Zabezpieczenia aparatów i urządzeń przed skutkami wybuchu pyłu
Masz chwilę?
Poznaj naszą ofertę szkoleń
Przeprowadziliśmy już setki szkoleń. Nasi eksperci, to praktycy którzy od lat realizują projekty dla branży przemysłowej. Decydując się na nasze szkolenia możesz mieć pewność, że wiemy o czym mówimy. To naprawdę rzadkość. Realizujemy zarówno szkolenia otwarte dla szerszego grona odbiorców oraz zamknięte, dostosowane do specyfiki konkretnej firmy.
Przyswajanie wiedzy w luźnej atmosferze? Nic prostszego! Za nami listopadowy czwartek z bezpieczeństwem

W ramach naszego nowego cyklu szkoleń pod nazwą „Czwartek z bezpieczeństwem” odbyło się pierwsze, listopadowe spotkanie. Odwiedzili nas m.in. przedstawiciele firm z branży farb i lakierów, chemicznej, zakładu produkującego materiały budowlane oraz producenta i dystrybutora gazów dla przemysłu.
Tematem przewodnim spotkania było Awaryjne oświetlenie ewakuacyjne i zapasowe obiektów zagrożonych wybuchem. Uczestnicy mogli zaczerpnąć wiedzy o systemach zasilania i sterowania oświetleniem w strefach, w których występuje zagrożenie wybuchem oraz na temat aktualnych wymogów prawnych i normatywnych w zakresie systemów oświetlenia awaryjnego (ewakuacyjne, zapasowe). Ponadto rozmawiano o sposobach testowania i rozwiązaniach technicznych opraw i układów zasilania w oparciu o normę PN-EN 50172.
Formuła szkolenia bardzo się sprawdziła – temat spotkania był bardzo interesujący, a dodatkowo swobodny sposób prowadzenia prezentacji spowodował, że uczestnicy chętnie zadawali pytania i wymieniali się doświadczeniami.
W ramach czwartku z bezpieczeństwem zaprosiliśmy zainteresowanych do naszego działu prefabrykacji skrzynek i paneli sterujących EX oraz do auta demonstracyjnego, w którym zaprezentowaliśmy urządzenia elektrotechniczne do pracy w strefach zagrożenia wybuchem.
Tematyka każdego ze spotkań czwartkowych obejmować będzie inne zagadnienia z branży przemysłowej. Jesteśmy przekonani, że każdy znajdzie dla siebie coś interesującego. Zachęcamy do zapoznania się z harmonogramem kolejnych spotkań.
Poznaj harmonogram kolejnych czwartków z bezpieczeństwem
Zobacz zdjęcia ze spotkania
Ocena Ryzyka Wybuchu dla linii do produkcji tytoniu w torebkach
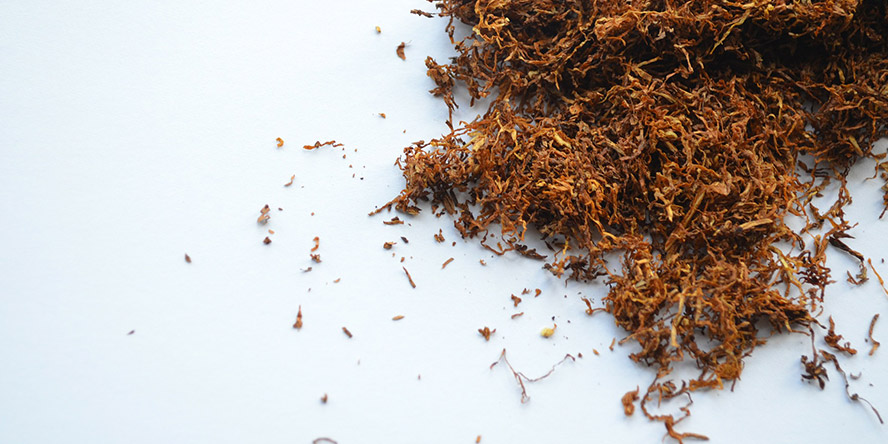
W ostatnim czasie na zlecenie producenta tytoniu nasi specjaliści ds. bezpieczeństwa wybuchowego wykonali Ocenę Ryzyka Wybuchu. Analiza dotyczyła głównie linii do produkcji tytoniu w torebkach oraz procesu łączenia tytoniu z dodatkami smakowymi. Celem audytu było zwiększenie poziomu bezpieczeństwa na terenie obiektu produkcyjnego.
W obszarze analizowanych instalacji wykorzystywane są m.in. kwas octowy oraz czysty alkohol etylowy, które mogą w określonych warunkach tworzyć atmosferę wybuchową. W Ocenie Ryzyka Wybuchu szczególnie istotna była analiza warunków, w których magazynuje oraz użytkuje się substancje palne. Przykładowo najniższa temperatura zapłonu alkoholu etylowego wynosi zaledwie 16°C. Również niska wartość minimalnej energii zapłonu stanowi poważne zagrożenie zapłonem, nawet od iskier ze słabych wyładowań elektrostatycznych, iskier spowodowanych uderzeniem mechanicznym bądź powstających w wyniku tarcia materiałów.
Ocenie zostały poddane następujące obszary obiektu:
- stanowisko magazynowania substancji stosowanych do produkcji dodatków smakowych,
- stanowisko do przygotowania dodatków smakowych,
- obszar dozowania substancji i dodatków smakowych do krajanki tytoniowej wraz z instalacją odciągu oparów z bębna mieszającego oraz znad krajanki tytoniowej.
Po dokonanej Ocenie Ryzyka Wybuchu eksperci zalecili montaż dodatkowego systemu badającego stężenie gazów w pomieszczeniu odpowiedzialnym za składowanie substancji stosowanej podczas produkcji tytoniu w torebkach oraz wskazali na ogólne działania w zakresie eksploatacji pomieszczeń i maszyn związanych z produkcją.
Opracowanie zostało sporządzone w ramach dostosowania, do wymogów prawa polskiego oraz unijnego.
Szukamy diamentów… mogą być nieoszlifowane
Szukamy diamentów… mogą być nieoszlifowane
Ciągły rozwój sprawia, że nieustannie poszukujemy nowych członków naszego zespołu. Jeśli szukasz więc wyzwań w firmie, która wyróżnia się płaską strukturą (na spotkanie ze mną nie musisz umawiać się poprzez sekretarkę, wystarczy jeśli zaczepisz mnie w biurze) i chce podbijać międzynarodowe rynki, to koniecznie aplikuj: www.grupa-wolff.eu/kariera.
Dla niewtajemniczonych – nasze działania obejmują pięć podstawowych obszarów: bezpieczeństwo wybuchowe, bezpieczeństwo procesowe, budowa instalacji przemysłowych w systemie „pod klucz”, dostawy i produkcja urządzeń procesowych dla materiałów sypkich oraz substancji ciekłych, transfer nowoczesnych technologii.
Ps. nie będę zakrzywiał rzeczywistości. Praca w GRUPIE WOLFF nie jest łatwa ale z pewnością satysfakcjonująca. Chcemy się rozwijać, kreować nowe standardy i budować polską markę. Wszystko to w duchu współpracy i zaufania.
FIRMA Z LUDZKĄ TWARZĄ
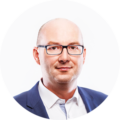
Nie chcemy być kolejną anonimową firmą…
Nie chcemy być kolejną anonimową firmą, opartą na powierzchownych relacjach typu fast-food. W biznesie szukamy czegoś więcej – zaufania, partnerstwa i ludzkiej twarzy. To na tych fundamentach chcemy budować GRUPĘ WOLFF. Nie jest to łatwe w świecie zdominowanym przez korporacyjny, chłodny styl prowadzenia biznesu. Zapewniam jednak, że będziemy starać się podążać własną drogą. Drogą biznesu z ludzką twarzą.
Dlatego, poprzez kanał na portalu LinkedIn oddaję się do waszej dyspozycji. Każdy z Was – klientów, partnerów, pracowników, a także potencjalnych pracowników czy klientów może zadać mi pytanie. Gwarantuje, że odpowiem na każde z nich.
Ze swojej strony będą chciał pokazywać Wam firmę od kuchni, udostępniać ciekawostki z branży, ciekawe konkursy oraz własne przemyślenia, czyli wszystko to co może Was zainteresować. Dołącz do mnie i bądźmy w kontakcie.
Dostawa i montaż instalacji systemów kominowych i odciągających dla jednego z najnowocześniejszych na świecie zakładów produkcyjnych w Brazylii
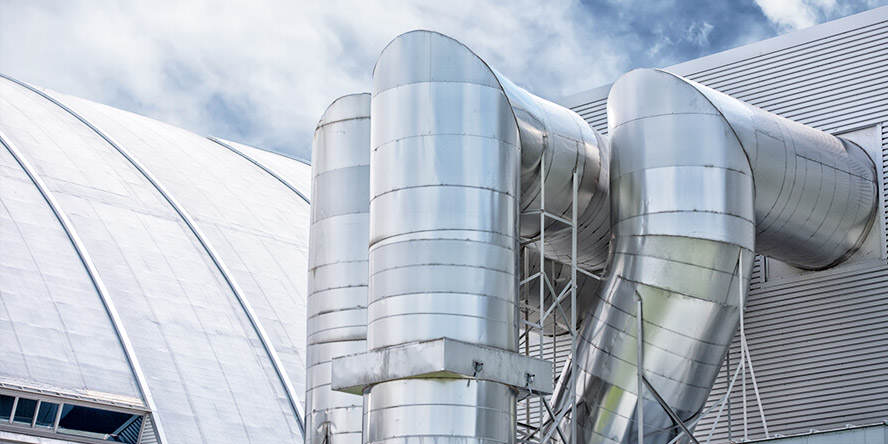
Dla jednego z naszych kluczowych Klientów zaprojektowaliśmy oraz wykonaliśmy instalacje odpylania dwóch linii produkcyjnych. Instalacja pracuje w jednym z najnowocześniejszych zakładów produkcyjnych na świecie, który zlokalizowany jest w Brazylii.
Zlecenie obejmowało wykonanie zaizolowanych instalacji kominowych z urządzeń technologicznych wraz z konstrukcjami wsporczymi. Dla każdego urządzenia technologicznego zrealizowano instalację odpylającą od króćca wylotowego z urządzenia po wyrzutnię zlokalizowaną na dachu hali.
W celu podparcia instalacji kominowych zaprojektowano i wykonano specjalne konstrukcje podporowe, mocowane do wiązarów dachowych wraz z gniazdami montażowymi. Każde przejście komina przez warstwę dachu zostało odpowiednio wykonane i uszczelnione.
Z urządzeń technologicznych zanieczyszczone powietrze jest odprowadzane przewodem elastycznym do separatorów cyklonowych. Następnie z cyklonów przewodami odpylającymi powietrze transportowane jest do wentylatorów promieniowych.
Zanieczyszczone powietrze trafia przewodami z okapów do wentylatorów promieniowych. Zapylone powietrze z wentylatorów odprowadzane jest przez wyrzutnię do atmosfery.
Wykonana przez nas instalacja stanowi niezbędny komponent dla pracy całego zakładu produkcyjnego. Jest to kolejna już inwestycja dla jednego z naszych kluczowych Klientów o zasięgu światowym.
Projekt w liczbach
- Przedsięwzięcie zrealizowaliśmy w odległości ponad 10 tys. km od naszego biura projektowego
Zlecenie objęło:
- 2 linie produkcyjne,
- 42 układy instalacji kominowych,
- 6 wentylatorów promieniowych,
- 4 wstępne separatory cyklonowe.
PREZENT: 3 darmowe miejsca na szkoleniu ATEX
PREZENT: 3 darmowe miejsca na szkoleniu ATEX
Dla osób, które do mnie napiszą i polecą mój wpis na profilu LinkedIn (link do wpisu) mam trzy darmowe miejsca na szkoleniu pt. Bezpieczeństwo produkcji w strefach zagrożenia wybuchem pyłów – zabezpieczenia przeciwwybuchowe oraz odpylanie instalacji przemysłowych. Szkolenie odbędzie się 07.12.17 w naszej siedzibie w podkrakowskich Balicach.
Wydarzenie realizujemy w ramach czwartków z bezpieczeństwem. Ta forma szkoleń wyróżnia się krótszą częścią wykładową, która skupia się na wąskim temacie oraz wyjątkowo długą częścią dyskusyjną. Całe spotkanie odbywa się w luźnej atmosferze sprzyjającej zadawaniu pytań i dyskusji. Wręcz zachęcamy uczestników do wcześniejszego informowania nas o problemach, które chcieliby omówić.
Zwieńczeniem wykładów i dyskusji jest wspólna kolacja, która odbywa się w pobliskim Skansenie Smaków (koszt kolacji pokrywa organizator, dojazd we własnym zakresie). W przededniu czwartku z bezpieczeństwem odbędzie się pełnowymiarowe szkolenie (www.hazex.eu/wydarzenia/szkolenie-atex-pyly-06-12-17) – proszę dać znać poprzez portal LinkedIn lub na adres biuro@hazex.eu, jeśli byliby Państwo zainteresowani udziałem także w tym wydarzeniu. W odpowiedzi prześlemy kod rabatowy obniżający cenę o 10%.
FIRMA Z LUDZKĄ TWARZĄ
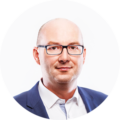
Nie chcemy być kolejną anonimową firmą…
Nie chcemy być kolejną anonimową firmą, opartą na powierzchownych relacjach typu fast-food. W biznesie szukamy czegoś więcej – zaufania, partnerstwa i ludzkiej twarzy. To na tych fundamentach chcemy budować GRUPĘ WOLFF. Nie jest to łatwe w świecie zdominowanym przez korporacyjny, chłodny styl prowadzenia biznesu. Zapewniam jednak, że będziemy starać się podążać własną drogą. Drogą biznesu z ludzką twarzą.
Dlatego, poprzez kanał na portalu LinkedIn oddaję się do waszej dyspozycji. Każdy z Was – klientów, partnerów, pracowników, a także potencjalnych pracowników czy klientów może zadać mi pytanie. Gwarantuje, że odpowiem na każde z nich.
Ze swojej strony będą chciał pokazywać Wam firmę od kuchni, udostępniać ciekawostki z branży, ciekawe konkursy oraz własne przemyślenia, czyli wszystko to co może Was zainteresować. Dołącz do mnie i bądźmy w kontakcie.
Młyny poziome
Ewakuacja jako priorytetowe zadanie ratownicze – część 4

Każde urządzenie, a przede wszystkim urządzenia przeciwpożarowe, tj. instalacje oświetlenia ewakuacyjnego, które stały się nimi w myśl rozporządzenia ministra spraw wewnętrznych i administracji1, powinny być poddawane okresowej konserwacji w celu eliminacji błędów i nieprawidłowości, jakie mogą powstać podczas eksploatacji. Okresowość takich badań opisuje również przytoczone rozporządzenie, które zostało opisane szerzej w poprzednich częściach artykułu.
W ustępie 3.2 rozporządzenia ministra spraw wewnętrznych i administracji wskazano, że urządzenia przeciwpożarowe i gaśnice przenośne powinny być poddawane przeglądom technicznym i czynnościom konserwacyjnym zgodnie z zasadami określonymi w Polskich Normach dotyczących urządzeń przeciwpożarowych i gaśnic, w dokumentacji techniczno-ruchowej oraz w instrukcjach opracowanych przez producentów. Idąc dalej, ustęp 3.3 zawiera zapis, że powyższe czynności powinny być prowadzone w taki sposób i w takich okresach, jakie są zgodne z instrukcją ustaloną przez producenta, nie rzadziej jednak niż raz w roku.
Biorąc pod uwagę oprawy i systemy oświetlenia ewakuacyjnego, producenci przystosowują swoje urządzenia do zapisów Polskiej Normy PN-EN 50172:2005. Systemy awaryjnego oświetlenia ewakuacyjnego. Ma to na celu zagwarantowanie poprawności ich działania podczas eksploatacji.
Ta sama norma została również przytoczona w rozporządzeniu i stała się wykładnią do prowadzonych na obiektach testów. Dokument ten posiada szereg zapisów dotyczących oświetlenia dróg ewakuacyjnych, powierzchni anypanicznych oraz stref wysokiego ryzyka i stanowi dopełnienie wymagań Polskiej Normy PN-EN 1838:2005/2011. Oświetlenie awaryjne.Wskazuje on, że sprzęt do awaryjnego oświetlenia ewakuacyjnego, a konkretnie oprawy (5.5.1) powinny być projektowane i konstruowane w sposób zgodny z normą EN-60598-2-22 (wymóg certyfikacji CNBOP), a w przypadku, gdy są one stosowane w strefach zagrożonych wybuchem, powinny być zgodne z normami dotyczącymi konstrukcji urządzeń w tych strefach oraz z dyrektywą ATEX.
W dalszej części dokument odnosi się bezpośrednio do sposobów serwisowania awaryjnego oświetlenia ewakuacyjnego i związanych z tym czynności. Odwołuje się do nich punkt 6., który wskazuje na potrzebę prowadzenia dziennika uwzględniającego rutynowe sprawozdania, testy, uszkodzenia i zmiany. Zapisy te mogą być prowadzone w formie raportu ręcznego lub otrzymane bezpośrednio z urządzenia w sposób automatyczny. W dobie wszechobecnej komputeryzacji coraz częściej wdraża się systemy kontrolno-wizualizacyjne, które zastępują dzienniki monitorowania układów oświetlenia awaryjnego. Systemy takie, oprócz kontroli i rejestracji zdarzeń wymaganych przez normę, mogą już sprostać wymaganiom w zakresie dostępu do rysunków instalacji, jakie powinny być przechowywane na terenie obiektu. W oprogramowaniu istnieje możliwość oznaczania pojedynczych opraw i podświetlanych znaków ewakuacyjnych oraz elementów systemu (np. czujniki kontroli napięcia), jakie w przypadku systemów baterii centralnej powinny być monitorowane i testowane. Daje to komfort pracy ze względu na możliwość prostej aktualizacji danych przy kolejnych zmianach w instalacji, co nie zawsze jest wykonywane w wersjach papierowych. Bardzo ważne jest, by dziennik raportów był dostępny dla każdej upoważnionej na obszarze obiektu osoby, np. służb utrzymania ruchu czy BHP, a przede wszystkim musi być okazywany podczas kontroli Państwowej Straży Pożarnej.

Minimalne zapisy, jakie należy prowadzić w Dzienniku Raportów dotyczą:
a) daty zamówienia systemu (wskazanie zapisu momentu uruchomienia),
b) daty każdego okresowego sprawdzania i testu,
c) daty i szczegółowych opisów każdego serwisu, testu czy sprawdzania,
d) daty i szczegółowych opisów sytuacji, w których nastąpiło uszkodzenie systemu, oraz informacji na temat prowadzonych prac mających na celu naprawę urządzeń,
e) daty i szczegółów każdej zmiany, jaka nastąpiła w instalacji podczas eksploatacji,
f) opisu charakterystyki pracy urządzeń samotestujących wykorzystywanych w instalacji.
Powyższe informacje powinny być opisywane w dzienniku w sposób zwięzły i zrozumiały, a wydruki z testowania urządzeń automatycznych powinny zawierać i spełniać wymagania zapisu normy. Dodatkowo takie dane jak czynności dotyczące wymiany źródeł światła, akumulatorów czy innych komponentów opraw również powinny znaleźć się w zapisach, co w strefach zagrożenia wybuchem jest bardzo istotne z punktu widzenia bezpieczeństwa prowadzonych prac. Punkt 7. normy w całości poświęcony jest zapisom dotyczącym serwisu oraz testowania urządzeń i zwraca uwagę na czynności oraz regularne poddawanie pracom konserwacyjnym elementów wchodzących w skład instalacji oświetlenia ewakuacyjnego. Osoba prowadząca prace serwisowe powinna posiadać odpowiednią wiedzę o systemie i oprawach. Niejednokrotnie poświadczeniem uprawnień do wykonania usługi zgodnie z instrukcją producenta jest autoryzacja. Urządzenia samotestujące powinny przeprowadzać testy nie rzadziej niż raz w miesiącu. Powinny być one zapisywane w ich pamięci lub wydrukowane do późniejszej archiwizacji wyników. W innym przypadku należy przeprowadzać testy według punktu 7.2 normy, a wyniki zapisywać ręcznie.
Testy opraw i systemów oświetlenia awaryjnego zostały podzielone na 3 okresy (codzienny, comiesięczny, coroczny) w zależności od czynności wymaganych do ich wykonania oraz rodzajów systemów zasilania opraw.
Test codzienny wymagany jest przy układach zasilania centralnego, a przeprowadzana inspekcja wzrokowa wskaźników ma rozpocząć gotowość systemu do pracy oraz ustalić, czy wskazania nie stanowią podstawy do przeprowadzenia testu. Systemy centralnej baterii posiadają możliwość kontroli poprzez wyświetlacz i wskaźniki świetlne znajdujące się na urządzeniu lub wyniesiony, np. do pomieszczenia dyspozytorni, panel kontrolny. Systemy komputerowe mają możliwość bezpośredniego wystawienia informacji o bieżącym stanie pracy poprzez sterownik główny, a operator podpięty do sieci przemysłowej takiej jak BACNet czy LONWorks może decydować w sposób zdalny o przeprowadzeniu testu.
Test comiesięczny zwany jest również testem krótkim i jeśli wykonywany jest automatycznie, to jego wynik musi być rejestrowany. W przypadku, gdy urządzenie w postaci modułu autotestu przeprowadziło test samoczynnie, a jego wynik został uwidoczniony w postaci sygnalizacji na kontrolkach LED modułu akumulatorowego (rys. 3), należy ten fakt zanotować. Jeśli pojawił się błąd urządzenia, musi być ono poddane dodatkowemu sprawdzeniu, łącznie ze źródłami światła, i gdy zaistnieje taka potrzeba, należy je wymienić na sprawne.
Należy zwrócić uwagę na proste układy opraw, w których kontrolka LED (zielona lub czerwona) wskazuje jedynie na obecność napięcia zasilania, a nie wyniku testu. Przykładowo urządzenia produkcji EATON Crouse-Hinds (CEAG) wyposażone są w układy autotestu, które podczas testu i po nim wyświetlają komunikat o stanie urządzenia, sygnalizowany przez kontrolki LED. Szczegółowe informacje dotyczące znaczenia odpowiednich sygnałów są podane w dokumentacji techniczno-ruchowej. Sygnały te mogą wskazywać dokładnie, czy uszkodzeniu uległ akumulator czy źródło światła. Dopiero na tej podstawie jesteśmy w stanie określić, czy urządzenie, jakim jest oprawa ewakuacyjna, jest w pełni sprawne i gotowe do dalszej eksploatacji ze znamionowymi parametrami pracy.
Test comiesięczny powinien być przeprowadzany podczas przejścia w pracę awaryjną każdej oprawy oświetleniowej znajdującej się na drogach ewakuacyjnych, strefach antypanicznych, strefach za wyjściami na zewnątrz lub w strefach wysokiego ryzyka. Dotyczy to również każdego podświetlanego znaku kierunku ewakuacji lub opraw, które doświetlają zarówno te znaki, jak i urządzenia przeciwpożarowe innych systemów bezpieczeństwa. Test ten ma symulować uszkodzenie zasilania podstawowego, a rolą sprawdzającego jest potwierdzenie, że każda z opraw została załączona do pracy awaryjnej. Zadaniem tego testu jest również zyskanie pewności, czy dana oprawa spełnia poprawnie swoją funkcję, ponieważ w procesie przemysłowym mogła przykładowo zostać uszkodzona, a w przypadku dużego zapylenia zabrudzona, przez co przewidziane w pierwotnych założeniach oświetlenie może być nieodpowiednie.

Zdarzają się sytuacje, gdy zmiany w konstrukcji urządzeń mogą być podstawą do zmiany lokalizacji lub dodania nowego źródła oświetlenia awaryjnego, koniecznego dla potrzeb ewakuacji lub procesu produkcyjnego. Przy stosowaniu układów centralnej baterii należy sprawdzić działanie systemu monitorowania wszystkich urządzeń wchodzących w skład instalacji zasilania i kontroli. Jeśli do zasilania używane są generatory, należy odnieść się do wymagań normy ISO 8528-12.
Zakończenie testów powinno odbyć się poprzez sprawdzenie urządzeń pod kątem przywrócenia ładowania zasilania podstawowego. Ze względu na liczbę opraw na terenie obiektu coraz częściej wybiera się systemy monitorowania centralnego. Podczas testu daje to przewagę nad rozwiązaniem indywidualnym pod kątem czasu trwania, możliwości pomyłki oraz liczby czynności, jakie należy przeprowadzić podczas testu comiesięcznego.
Układy monitorowania z określeniem adresu oprawy pozwalają na szybką lokalizację uszkodzenia i na stwierdzenie, z jakiego rodzaju uszkodzeniem mamy do czynienia (np. przepalone źródło światła, uszkodzony statecznik). Niewątpliwie jest to zaletą w wypadku rozległych obiektów i instalacji w strefach zagrożenia wybuchem, w trudnych warunkach pracy czy w trudno dostępnych miejscach, gdyż informacja zwrotna z systemu pozwala na szybką reakcję grupy serwisowej, podjęcie odpowiedniego sprzętu i części zamiennych, co jest bardzo pomocne w przypadku zleceń realizowanych przez firmy zewnętrzne. Za takim rozwiązaniem przemawiają również rachunek ekonomiczny i zapewnienie bezpieczeństwa dzięki szybkiemu zadziałaniu.
Test coroczny zwany jest inaczej testem długim. Tak jak wcześniejszy, również musi być zarejestrowany w przypadku występowania urządzenia samotestującego, a gdy jest ono wyposażone w układ autotestu, jego wynik należy zapisać ręcznie. Test coroczny jest rozszerzeniem testu comiesięcznego i powinien zawierać test sprawności źródła zasilania awaryjnego polegający na sprawdzeniu pełnego czasu trwania jego podtrzymania, zgodnie z informacją, jaką producent zamieścił na oprawie lub w systemie. Dodatkowo zaleca się sprawdzenie poprawności układu ładowania. W porównaniu z oprawami autonomicznymi w systemach z centralnym układem zasilania jest to czynność prosta, a dodatkowych informacji dostarcza opcjonalnie system nadzoru, który pokazuje, jaki prąd aktualnie płynie w obwodzie.
W przypadku każdego z testów należy wprowadzić ich datę oraz wynik, na co wskazuje wymaganie normy dotyczące zapisów dziennika. W praktyce trzeba również określić kolejny termin przeglądu. Jeśli jednak służby wymagają częstszego przeprowadzania badań (co jest zalecane w niektórych strefach zagrożenia wybuchem ze względu na czynniki otaczające oprawy lub występowanie stref wysokiego ryzyka), należy w porozumieniu ustalić i wyznaczyć inne terminy serwisów. Informacje w układach automatycznych mogą być zapisane do ich pamięci, dzięki czemu służby obsługujące system będą informowane o nadchodzących terminach wykonania testów.

UWAGA! Pełne testy, które prowadzą do rozładowania energii elektrycznej z akumulatorów powinny być przeprowadzane w okresach, w których występuje niskie ryzyko zagrożenia. Jeżeli wiemy o możliwie niebezpiecznej sytuacji, jaka może się pojawić w strefach zagrożenia wybuchowego, w szczególności w strefach 1 i 2, testy takie powinny być konsultowane i uzgadniane z grupą osób odpowiedzialnych za bezpieczeństwo i utrzymanie ruchu, tak aby czas na ponowne naładowanie (Centralna Bateria – 12 godz., indywidualne – 24 godz.) nie przebiegał w najgorszym momencie pracy w danym obszarze lub w momencie przebywania w nim dużej liczby osób.
Dobrym sposobem jest zaplanowanie i przeprowadzanie testów podczas remontów lub modernizacji innych instalacji, gdy strefa nie występuje lub jest mocno ograniczona – nawet jeżeli serwis systemu oświetlenia ewakuacyjnego przypada szybciej lub będzie częściej wykonywany. Podane normy i rozporządzenie określają okresy minimalne i nie muszą być one jedyną wykładnią, jeśli zarządca wyda decyzję o częstszych terminach przeprowadzania testów. Innym rozwiązaniem jest powołanie do testów serwisu, który posiada urządzenia i rezerwowe źródło akumulatorów na czas ich wykonywania. Pozwoli to na bezpieczne ponowne naładowanie akumulatorów i w przypadku awarii oświetlenia podstawowego poprawne doświetlenie stref ewakuacji.
1) Rozporządzenie Ministra Spraw Wewnętrznych i Administracji w sprawie ochrony przeciwpożarowej budynków, innych obiektów budowlanych i terenów z dnia 7 czerwca 2010 (Dz. U. z dnia 22 czerwca 2010 r.) powołane na mocy art. 13 ust. 1 i 2 ustawy z dnia 24 sierpnia 1991 r. o ochronie przeciwpożarowej (Dz. U. z 2009 r. Nr 178, poz. 1380 oraz z 2010 r. Nr 57, poz. 353).
Mikołaj zostawił dla Ciebie prezent
Mikołaj zostawił nam dla Ciebie prezent ![🙂]()
Jak co roku nasz dział od zadań specjalnych i rzeczy niemożliwych przygotował zabawę, do której was serdecznie zapraszamy. Wśród osób, które wezmą udział rozlosujemy kilkadziesiąt prezentów (Pakiety Piwne WOLFF PREMIUM BEER – idealne do przygotowania grzanego piwa, roczne prenumeraty Expressu Przemysłowego – idealne na zimowe wieczory, kalendarze książkowe – idealne na nowy rok). Pamiętajcie, to nie Totolotek – tu macie realną szansę na zwycięstwo. Do dzieła!
Co dla Ciebie ma Mikołaj

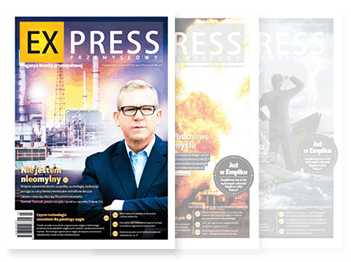
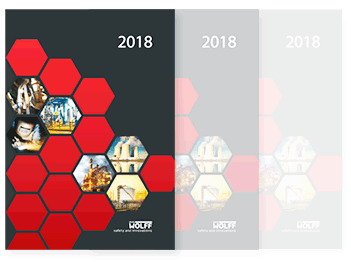
10 x Unikatowy Pakiet Piwny WOLFF PREMIUM BEER z niszowymi, rzemieślniczymi piwami
10 x Roczna prenumerata Expressu Przemysłowego – czasopismo ludzi przemysłu
10 x Kalendarz książkowy na 2018 rok – niezbędny w codziennej pracy
Jak zgarnąć prezent
To bardzo proste. Ponieważ liczba prezentów jest ograniczona, Święty Mikołaj przygotował pewną zabawę. Udowodnij, że upominek należy się właśnie Tobie i napisz w liście do Mikołaja czym zasłużyłeś, aby go dostać.
Napisz list do Św. Mikołaja
Podaj nam także adres na jaki mamy wysłać prezent. Do dzieła!
WYBUCH PYŁU CUKRU – film z testów oraz konkurs. Wygraj udział w szkoleniu ATEX
WYBUCH PYŁU CUKRU – film z testów oraz konkurs. Wygraj udział w szkoleniu ATEX
W czwartek 7 grudnia, w ramach szkolenia ATEX, sprawdziliśmy jak wybucha pył cukru – efekty możecie zobaczyć na filmie poniżej (konkurs znajduje się na końcu wpisu).
Instalacja składa się z dwóch zbiorników o wymiarach 37x37x37 cm (V=50l) połączonych kanałem. W obu komorach znajduje się niewielka ilość pyłu cukrowego, który zostaje wzbudzony poprzez podmuch powietrza. W chwili kontaktu chmury z gorącą powierzchnią (rozgrzany pręt w prawej komorze) dochodzi do zapłonu i wybuchu. Ciśnienie i ogień przebijają się do lewego zbiornika, gdzie dochodzi do wybuchu wtórnego. Oba zbiorniki są zabezpieczone poprzez „panele dekompresyjne” wykonane z warstwy aluminium i papieru, które uległy rozerwaniu, pozwalając ujść skutkom wybuchu (ciśnienie, ogień) do atmosfery. Mimo, że skala testu (w porównaniu do warunków przemysłowych) była mikroskopijna płomienie sięgały kilku metrów, a uczestnicy pokazu wyraźnie odczuli falę ciśnienia i ciepła.
KONKURS: dlaczego w rzeczywistych warunkach przemysłowych na kanale łączącym oba zbiorniki należy zamontować tzw. izolację wybuchu, która uniemożliwi przebicie się płomienia do sąsiedniego zbiornika? Wśród osób, które odpowiedź prawidłowo rozlosujemy trzy szkolenia ATEX: www.hazex.eu/szkolenia-atex/czwartek-z-bezpieczenstwem
FIRMA Z LUDZKĄ TWARZĄ
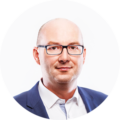
Nie chcemy być kolejną anonimową firmą…
Nie chcemy być kolejną anonimową firmą, opartą na powierzchownych relacjach typu fast-food. W biznesie szukamy czegoś więcej – zaufania, partnerstwa i ludzkiej twarzy. To na tych fundamentach chcemy budować GRUPĘ WOLFF. Nie jest to łatwe w świecie zdominowanym przez korporacyjny, chłodny styl prowadzenia biznesu. Zapewniam jednak, że będziemy starać się podążać własną drogą. Drogą biznesu z ludzką twarzą.
Dlatego, poprzez kanał na portalu LinkedIn oddaję się do waszej dyspozycji. Każdy z Was – klientów, partnerów, pracowników, a także potencjalnych pracowników czy klientów może zadać mi pytanie. Gwarantuje, że odpowiem na każde z nich.
Ze swojej strony będą chciał pokazywać Wam firmę od kuchni, udostępniać ciekawostki z branży, ciekawe konkursy oraz własne przemyślenia, czyli wszystko to co może Was zainteresować. Dołącz do mnie i bądźmy w kontakcie.
Dostawa systemów przeciwwybuchowych typu HRD do zabezpieczenia instalacji formowania płyt wiórowych
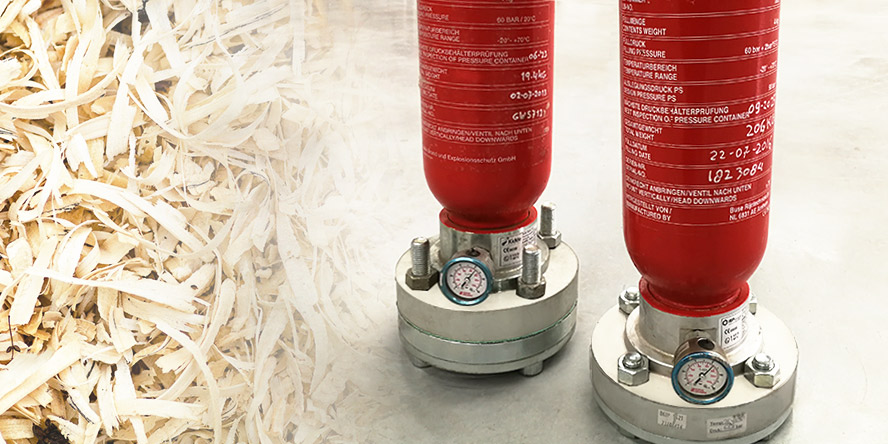
Dla jednego z największych producentów mebli w Europie GRUPA WOLFF dostarczyła zabezpieczenia przeciwwybuchowe w postaci systemów izolacji (odsprzęgania) wybuchu typu HRD.
Ryzyko tworzenia pyłowej atmosfery wybuchowej w zakładzie związane jest z obecnością pyłu drzewnego. Systemy HRD zostały zastosowane na nowej instalacji formowania płyt wiórowych, która budowana jest w celu produkcji płyt meblowych na potrzeby własne zakładu.
Poszczególne urządzenia takie jak silosy, filtry, cyklony, filtro-cyklony oraz przesiewacze zabezpieczono poprzez układy odpowietrzania wybuchu. Na układach transportu tj. na rurociągu, przesypach i przenośnikach zgrzebłowych zabudowano systemy izolacji typu HRD, które po wykryciu wybuchu w ciągu kilkudziesięciu milisekund wprowadzą do układu transportu proszek tłumiący, w wyniku czego fala wybuchu zostanie zatrzymana, a płomień zgaszony. Dzięki temu rozwiązaniu zarówno urządzenia jak i cała instalacja zostały zabezpieczone przed skutkami ewentualnego wybuchu i jego propagacji.
Zlecenie zrealizowano w wersji „pod klucz” – GRUPA WOLFF wykonała zakres prac, który obejmował:
- projekt,
- dostawy systemów,
- prace pre-instalacyjne elektryczne i mechaniczne,
- montaż,
- uruchomienie z przekazaniem do ruchu wraz dokumentacją powykonawczą,
- opieka serwisowa gwarancyjna i pogwarancyjna.
W ciągu kilku ostatnich kilku miesięcy w przemyśle drzewnym doszło do kilku przypadków wybuchów i pożarów, dlatego zasadne jest, by producenci zwrócili uwagę na problem jaki niesie za sobą występowanie palnych pyłów oraz podejmowali działania mające na celu ochronę nie tylko instalacji produkcyjnych, ale również zdrowia i życia pracowników.
Alternatywne podejście do oceny ryzyka wybuchu – pyły

dr. hab. inż. Andrzej Wolff | ATEX WOLFF i Wspólnicy sp.j. (GRUPA WOLFF)
I. Ograniczenia wynikające ze stosowania oceny ryzyka wybuchu
Konieczność przeprowadzenia oceny ryzyka wybuchu w warunkach produkcji zagrożonej obecnością palnych i wybuchowych gazów, pyłów, mgieł, par palnych cieczy i włókien wynika z zapisów dyrektywy europejskiej Atex 137 (99/92/WE), a w warunkach polskich z zapisów Rozporządzenia Ministra Gospodarki z 8 lipca 2010 r. w sprawie minimalnych wymagań, dotyczących bezpieczeństwa i higieny pracy, związanych z możliwością wystąpienia w miejscu pracy atmosfery wybuchowej (Dz. U. 2010 nr 138 poz. 931) [1].
Ocena ryzyka wybuchu związana z możliwością wystąpienia w miejscach pracy atmosfery wybuchowej, zgodnie z [1], powinna brać pod uwagę:
• prawdopodobieństwo i czas występowania atmosfery wybuchowej;
• prawdopodobieństwo wystąpienia oraz uaktywnienia się źródeł zapłonu, w tym wyładowań elektrostatycznych;
• eksploatowane przez pracodawcę instalacje, używane substancje i mieszaniny, zachodzące procesy i ich wzajemne oddziaływania.
Ocena ryzyka wybuchu oparta o występowanie atmosfery wybuchowej i potencjalnych źródłach zapłonu oraz znajomości procesu zostanie w dalszej części pracy poddana weryfikacji.
Zostanie również przedstawiona nowa koncepcja oceny ryzyka, która nacisk kładzie nie tylko na czynniki podane wyżej, ale ponadto na stosowane typowe operacje jednostkowe, konstrukcję i warunki pracy aparatów oraz własności stosowanych w procesie substancji i ich mieszanin.
Do oceny ryzyka wybuchu na podstawie identyfikacji zagrożeń, z oszacowaniem ryzyka, standardowo wykorzystywane jest podejście jakościowe. Jest to usystematyzowane podejście, które w połączeniu z wiedzą i doświadczeniem osób wykonujących ocenę powinno zapewnić identyfikację zagrożeń [2]. Identyfikacja zagrożeń i ocena ryzyka, wg [2], są prowadzone w oparciu o arkusze robocze i matrycę ryzyka R. Podczas przeprowadzania oceny ryzyka wykorzystuje się tabele 1 i 2, a do określenia poziomu zagrożeń (akceptowalności ryzyka) matrycę podaną w tabeli 3.
Tabela 1. Kategoria częstotliwości wystąpienia efektywnych źródeł zapłonu P, które mogą spowodować wybuch
Tabela 2. Określenie skutków wybuchu S
Ryzyko „R” wynika z przyjętych wartości P i S, z tabeli 1 i 2, oraz równania: R = P x S, gdzie:
R – ryzyko zdarzenia,
P – częstotliwość zdarzenia (wystąpienia efektywnego źródła zapłonu),
S – skutki, jakie mogą wystąpić, gdy dojdzie do wybuchu.
Na podstawie wyznaczonej wartości ryzyka R i matrycy ryzyka, tabela 3, szacujemy poziom akceptowalności ryzyka.
Tabela 3. Matryca ryzyka
Podejście to bierze pod uwagę następujące poziomy ryzyka:
A – ryzyko wysokie – nieakceptowalne – konieczne działania techniczne i/lub konstruktywne* zmniejszające poziom ryzyka;
B – ryzyko wysokie – konieczne podjęcie działań technicznych i rozważenie celowości podjęcia działań konstruktywnych obniżających poziom ryzyka;
C – ryzyko średnie – zalecane podjęcie działań technicznych i organizacyjnych obniżających poziom ryzyka;
D – ryzyko małe (pomijalne) – podjęcie działań obniżających poziom ryzyka nie jest wymagane.
Identyfikacja zagrożeń z oszacowaniem ryzyka wybuchu R na podstawie pojęcia częstotliwości/prawdopodobieństwa skali zdarzenia S i częstotliwości/prawdopodobieństwa występowania efektywnych źródeł zapłonu P może jednak nie doprowadzić do prawidłowej oceny sytuacji, gdyż jest w dużym stopniu oparta na subiektywnej ocenie. Między innymi, należy zdecydować, jaką wartość kategorii P (częstotliwość występowania źródeł zapłonu) lub kategorii S (skala skutków zdarzenia) trzeba przyjąć, w danej sytuacji procesowej, by oszacować ryzyko R. Nie jest to zadanie proste, i to nie tylko ze względu na subiektywny charakter oceny.
Uzyskana wartość ryzyka R prowadzi do zakwalifikowania ryzyka do określonej grupy; tabela 3: ryzyko nieakceptowalne A (kolor czerwony), wysokie B (żółty), średnie C (zielony) i pomijalne D (czarny). Takie zdefiniowanie ryzyka prowadzi do kolejnej arbitralnej decyzji –jakie działania korekcyjne, w celu dostatecznego zmniejszenia ryzyka R, należy zastosować w stosunku do pojedynczego aparatu czy węzła procesowego. W praktyce mamy do dyspozycji podjęcie działań o charakterze technicznym (zasadniczo poprawiających bezpieczeństwo procesowe), konstruktywnym (poprawiających stopień zabezpieczenia przed skutkami wybuchu) i organizacyjnym.
W trakcie prowadzenia oceny ryzyka zwykle pojawia się problem interpretacji, szczególnie ryzyka wysokiego B i nieakceptowalnego A. Bo co oznacza w praktyce ryzyko nieakceptowalne A i na podstawie jakich kryteriów możemy przyjąć ten poziom? Czy w przypadku kwalifikacji ryzyka do poziomu nieakceptowalnego A należy podjąć decyzję o bezzwłocznym zatrzymaniu pracy instalacji? Nie jest to łatwy wybór gdyż, między innymi, będzie się wiązać z konsekwencją nieraz dużych strat w produkcji. Z tego powodu podejmowanie decyzji o przyjęciu ryzyka na poziomie A powinno wynikać z jasnych przesłanek, a te z oczywistych stwierdzonych zagrożeń i zaniedbań w zakresie zapewnienia bezpieczeństwa wybuchowego.
Innego typu problemy mamy w przypadku ryzyka wysokiego B. Czy każdorazowo wymaga ono podjęcia działań konstruktywnych i technicznych, czy nie? Czy w pewnych sytuacjach nie wystarczy tylko zastosowanie działań technicznych i rozważenie konieczności podjęcia działań konstruktywnych? Na podstawie jakich kryteriów mamy o tym decydować?
Ponadto nie wszystkie aparaty procesowe można zabezpieczać przed wybuchem, mimo tego że ich działanie, konstrukcja i stosowane substancje (własności palne i wybuchowe pyłów) oraz obecność potencjalnych źródeł zapłonu stwarzają wysoki poziom zagrożenia. Dotyczy to głównie aparatów, które konstrukcyjnie nie są dostatecznie szczelne (np. przesiewacze, granulatory, młyny [często]).
W celu ograniczenia tego typu problemów można zaproponować modyfikację schematu oceny ryzyka wysokiego B. Zakłada ona podział grupy ryzyka wysokiego na dwie podgrupy B1 i B2. W efekcie zaproponowany plan działań naprawczych przedstawia się jak poniżej:
A – ryzyko wysokie nieakceptowalne – konieczne bezzwłoczne podjęcie działań technicznych, przeciwwybuchowych* i organizacyjnych w celu zmniejszenia poziomu ryzyka;
B1 – ryzyko wysokie – konieczne podjęcie działań technicznych i konstruktywnych* obniżających poziom ryzyka;
B2 – ryzyko wysokie – konieczne podjęcie działań technicznych i rozważenie celowości podjęcia działań konstruktywnych* obniżających poziom ryzyka;
C – ryzyko średnie – zalecane podjęcie działań technicznych i/lub organizacyjnych obniżających poziom ryzyka;
D – ryzyko małe (pomijalne) – podjęcie działań obniżających poziom ryzyka nie jest wymagane.
Poziom B1 ukierunkowany jest raczej na zagrożenia wywołane obecnością palnych i wybuchowych pyłów. Natomiast poziom B2 będzie miał częściej zastosowanie w przypadku zagrożeń wywołanych obecnością palnych i wybuchowych gazów i par palnych cieczy. Czy rozwiązuje to problem dostatecznej dokładności matrycy ryzyka? Niestety nie, ale lepiej precyzuje zasadność stosowania środków technicznych i konstruktywnych w obszarze wysokiego poziomu ryzyka B.
A jak postępować w przypadku, gdy mamy do czynienia z substancją palną i wybuchową, jaką jest np. sadza charakteryzująca się wysoką wartością MEZ? Z dostępnych danych wynika, że wartość MEZ sadzy > 10 000 mJ. Dostępne są także dane, dla których wartość MEZ > 1000 mJ, a więc jest ona kilkukrotnie mniejsza. Szczególnie w przypadku pierwszym ryzyko zapłonu sadzy jest generalnie bardzo małe. Pojawia się więc problem, jaką należy przyjąć wartość kategorii P z tabeli 1 w celu określenia ryzyka R. Przyjęcie wartości P = 2 (mało prawdopodobne, ale może wystąpić w okresie użytkowania) prowadzi do poziomu ryzyka B (ryzyko wysokie – konieczne podjęcie działań konstruktywnych i rozważenie celowości podjęcia działań technicznych obniżających poziom ryzyka). Natomiast przyjęcie wartości P = 1 (bardzo mało prawdopodobne, ale jednak możliwe) prowadzi do poziomu ryzyka C (ryzyko średnie – zalecane podjęcie działań technicznych i/lub organizacyjnych obniżających poziom ryzyka). Arbitralne przyjęcie wartości B lub C będzie miało poważne konsekwencje finansowe związane z koniecznością zastosowania określonych rozwiązań mających na celu ograniczenie ryzyka.
Typowa ocena ryzyka wybuchu, sporządzona w oparciu o procedurę wyznaczania wartości liczbowej ryzyka R, bierze pod uwagę możliwy skutek wybuchu S (tabela 2). Szacowanie wartości S oparte jest na opisowej definicji skali możliwych skutków zdarzenia (katastroficzne, poważne, drobne, pomijalne) oraz na charakterystyce następstw (ofiary śmiertelne…, ciężkie urazy pracowników…, lekkie obrażenia pracowników…, nieznaczne obrażenia pracowników…). Alternatywnie stosowane jest także podejście do określenia skutków S na podstawie szacowania skali możliwych finansowych strat.
Jak jednak przewidzieć, i na podstawie jakich kryteriów, kiedy może dojść do skutków katastroficznych? I co to pojęcie w gruncie rzeczy oznacza? Przyjęcie określonej wartości straty finansowej ma tak samo subiektywny charakter i zależy od indywidualnej oceny sytuacji. Straty rzędu 1 mln zł, spowodowane wybuchem, w zakładzie o wartości produkcji rzędu 100 mln zł raczej nie są katastroficzne, ale dla firmy o przerobie 10 mln zł już (raczej) będą. Ponadto pojęcie strat finansowych nie uwzględnia ryzyka zagrożenia zdrowia i życia pracowników. A przecież jest to wartość nadrzędna.
Z podobnymi problemami mamy do czynienia w przypadku podejścia opierającego się na definicji częstości zdarzenia (tabela 4). Wykorzystuje ono matrycę ryzyka podaną w tabeli 3. Podejście to nie wnosi jednak nic nowego w zakresie precyzji wyznaczania ryzyka na podstawie subiektywnej oceny sytuacji.
Tabela 4. Powiązanie częstości wystąpienia efektywnych źródeł zapłonu, które mogą spowodować wybuch, z prawdopodobieństwem wystąpienia atmosfery wybuchowej w celu określenia częstości występowania zagrożeń wybuchowych
II. Wpływ czynników procesowych na ocenę ryzyka wybuchu
W stosowanej obecnie metodologii oceny ryzyka wybuchu wprowadzono mało precyzyjne pojęcie prawdopodobieństwa [1] i trudne do ilościowego oszacowania pojęcie częstotliwości występowania potencjalnego źródła zapłonu [2]. Niewątpliwie częstość występowania efektywnych źródeł zapłonu jest bardzo istotna, a nawet kluczowa. Ale czy jest to jedyne istotne zagrożenie, które należy brać pod uwagę? I jak odnieść definicję częstości wystąpienia efektywnych źródeł zapłonu (tabela 1: występuje bardzo często, może występować często czy mało prawdopodobne, ale może wystąpić w okresie użytkowania) do realnych sytuacji, z którymi mamy do czynienia w przemyśle? W praktyce według naszej oceny należałoby także brać pod uwagę stosowane substancje sypkie (własności fizyko-chemiczne pyłów). A szczególnie wartość minimalnej energii zapłonu MEZ. Im wyższa jest wartość MEZ, tym lista potencjalnych źródeł zapłonu (w sensie realnego zagrożenia) maleje. Na przykład dla pyłów węgla kamiennego, dla którego MIE > 1000 mJ, zagrożenie spowodowane typowymi iskrowymi i snopiastymi wyładowaniami elektrostatycznymi nie jest brane pod uwagę. Podobnie będzie w przypadku, omawianej wcześniej, sadzy. Ale już w przypadku pyłów węgla brunatnego sytuacja jest zdecydowanie inna.
Nawet jednak gdy wartość MIE pyłu jest (stosunkowo) niska, co oznacza, że liczba potencjalnych źródeł zapłonu może rosnąć, to nie znaczy, że w aparacie musi dojść do wybuchu.
Czynnikiem determinującym jest także rodzaj prowadzonej operacji jednostkowej, typ i konstrukcja aparatu, jego objętość robocza oraz kształt. Szczególnie istotna jest konstrukcja aparatu, a w praktyce jego smukłość (stosunek średnicy do wysokości). Wiadomo przecież, że w przypadku smukłych aparatów (silosów, zbiorników, podajników kubełkowych) zagrożenie zapłonem spowodowane tarciem i ładowaniem się elektrostatycznym opadających cząstek (o siebie i o ścianę aparatu) prowadzi do istotnego nagromadzenia się na ich powierzchni elektryczności statycznej. Rośnie także zagrożenie iskrą mechaniczną wskutek obecności ewentualnych zanieczyszczeń (kamienie, drobne elementy metalowe, np. rdza) w podawanym z dużej wysokości lub na dużą wysokość materiale. To pierwsze dotyczy szczególnie sytuacji zasypywania pustego silosu/zbiornika podczas uruchomienia instalacji po okresowym przeglądzie, remoncie czy awarii.
Nawet gdy określimy, które źródła zapłonu mogą być obecne (np. zbyt wysoka temperatura powierzchni aparatu), to jak wyznaczyć wiarygodnie częstotliwość występowania tego potencjalnie efektywnego źródła zapłonu? Zbyt wysoka temperatura powierzchni aparatu może oczywiście wynikać z warunków prowadzenia procesu. W takiej sytuacji konieczna jest analiza stosowanej technologii i wykorzystywanych aparatów w celu eliminacji (ograniczenia) wpływu tego czynnika.
Zbyt wysoka temperatura powierzchni jest możliwa i szczególnie niebezpieczna w stanie awaryjnym – np. zatarcie łożyska. Tylko jak oszacować, jak często może do tego zdarzenia dojść? A ponadto ocena ryzyka wybuchu zajmuje się warunkami normalnej pracy (zatrzymanie, praca, rozruch), a nie stanami awaryjnymi… Jak w praktyce odciąć się od typowych i znanych stanów awaryjnych w ocenie sytuacji? Są one przecież w sposób naturalny związane z produkcją. Tylko jak to uwzględnić w ocenie sytuacji? Skąd mamy wiedzieć, kiedy może dojść do przegrzania elementu aparatu (np. z powodu niezadziałania czujnika [termopary])? A iskry mechaniczne – jak możemy ilościowo określić zagrożenie w podajniku kubełkowym z powodu uszkodzenia łożyska wałka (stan awaryjny) i w konsekwencji przesunięcia taśmy transportującej materiał sypki w kubełkach oraz jej tarcie o ścianę aparatu prowadzące do bardzo niebezpiecznego iskrzenia?
Istotny jest także typ stosowanych operacji jednostkowych oraz charakter przepływu materiałów. Na przykład transport mechaniczny (z wyłączeniem podajników kubełkowych) typowo zapewnia warunki laminarnego przemieszczania materiałów sypkich i zawartych w nich pyłów. Zagrożenia, wynikające z konstrukcji i zasady działania podajnika, są więc w takim przypadku ograniczone. Natomiast szereg innych operacji jednostkowych przebiega w aparatach, w których z racji konstrukcji i zasady działania mamy do czynienia z ruchem burzliwym materiału sypkiego i tym bardziej zawartych w nim pyłów, jak np. podajniki kubełkowe, filtry, silosy, cyklony. Ruch burzliwy materiałów, często konieczny z powodów procesowych, na ogół powoduje zwiększenie zagrożeń i tym samym ryzyka.
Dostępne normy zwykle nie biorą pod uwagę możliwej obecności mieszanin hybrydowych (mieszanina palnych pyłów oraz gazów i/lub par cieczy palnych). Wiedza techniczna i naukowa o wynikających z tego zagrożeniach jest ograniczona, mimo że zapłon i wybuch mieszaniny hybrydowej może prowadzić do bardzo poważnych konsekwencji. Rozporządzenie [1] i raport [2] nie biorą pod uwagę tego, realnego w wielu sytuacjach procesowych, zagrożenia zupełnie. W normie dotyczącej wyznaczania stref zagrożenia wybuchem dla gazów i par cieczy [4], jak i w normie dotyczącej wyznaczania stref zagrożenia wybuchem dla pyłów [5] zagadnieniu temu jest poświęcona tylko jedna strona bardzo ogólnego opisu.
Mimo zasygnalizowanych problemów w wielu praktycznych sytuacjach procesowych stosunkowo łatwo jest określić, które czynniki mogą powodować realne zagrożenie zapłonem, i tym samym można próbować je wyeliminować lub istotnie ograniczyć. Dotyczy to zaleceń technicznych ograniczających zagrożenia procesowe prowadzące do zapłonu. Gdy jednak podjęte środki techniczne nie zapewniają dostatecznego ograniczenia poziomu zagrożeń, to należy podjąć decyzję o zastosowaniu konstruktywnych technik zabezpieczania aparatów procesowych przed skutkami wybuchu. Tylko takie rozwiązanie pozwala nam uniezależnić się od problemów podanych wyżej.
III. „Bezpieczna” pojemność robocza aparatu
Kolejnym bardzo istotnym czynnikiem jest pojęcie „bezpiecznej” objętości roboczej aparatu. Czy objętość robocza równa np. 1 m3 stwarza realne zagrożenie i powoduje poważne konsekwencje w przypadku wybuchu, czy jeszcze nie? Zarówno wiedza naukowa, jak i praktyka przemysłowa są w tym zakresie ograniczone. Tak więc od jakiej objętości roboczej aparatu należy brać pod uwagę realne zagrożenie wynikające z zapłonu i wybuchu? Nie bardzo wiadomo.
Na przykład norma NFPA 652 [3] rekomenduje ochronę aparatu procesowego już nawet dla objętości roboczej 0,2 m3, uznając, że w tych warunkach spalanie deflagracyjne (spalanie rozprzestrzeniające się z prędkością poddźwiękową) może prowadzić do poważnego zagrożenia. Ale czy to oznacza, że już przy tak małych objętościach roboczych należy zabezpieczać aparaty przed skutkami wybuchu? Z naszych doświadczeń wynika, że taka szacunkowa objętość robocza powinna wynosić więcej. I zależy to od szeregu omówionych wcześniej czynników. Związana jest z tym na przykład smukłość aparatu. Stosunkowo łatwiejsze do ochrony przed skutkami wybuchu są aparaty o zbliżonej wartości wysokości L do średnicy D (aparaty o smukłości ok. 1). Zagrożenia rosną wraz ze wzrostem stosunku L/D i oczywiście z wzrostem objętości roboczej.
W praktyce należałoby więc brać pod uwagę, podczas oceny ryzyka wybuchu, szereg istotnych technicznych czynników, a nie tylko potencjalne źródła zapłonu, by oszacowany poziom ryzyka R był realny.
IV. Szacowanie ryzyka wynikającego z zagrożenia przeniesienia się wybuchu z aparatu procesowego na sąsiednie urządzenia
W przypadku stosowania typowej procedury oceny ryzyka wybuchu na podstawie podejścia jakościowego [2] szczegółowa analiza zagrożeń i konsekwencji nie jest możliwa. Bo podejście to nie bierze pod uwagę szeregu czynników omówionych powyżej, poza potencjalnymi źródłami zapłonu. Co więc należałoby zrobić, by procedura oceny ryzyka wybuchu uwzględniała nie tylko źródła zapłonu, ale także własności pyłu (MEZ), charakter ruchu pyłów (burzliwy/laminarny), konstrukcję aparatu (smukłość, objętość robocza) czy przeznaczenie aparatu (rodzaj operacji jednostkowej)?
Z praktyki przemysłowej wiadomo, że do aparatów szczególnie zagrożonych zapłonem i wybuchem ze względu na ich konstrukcję i warunki prowadzenia procesu należy zaliczyć: silosy/zbiorniki (magazynowanie jako operacja jednostkowa), filtry (odpylanie), podajniki kubełkowe (transport mechaniczny), młyny (mielenie) czy suszarnie (suszenie). W naszej opinii ponad 50% wybuchów w przemyśle ma swój początek w tego typu aparatach procesowych.
Według naszej wiedzy i w oparciu o lata doświadczeń w zabezpieczaniu aparatów i instalacji produkcyjnych przed skutkami wybuchu podejście oparte o ocenę zdolności pyłu do zapłonu i wybuchu, potencjalne źródła zapłonu, rodzaj operacji jednostkowej i konstrukcję aparatu pozwoliłoby na dużo bardziej precyzyjną ocenę sytuacji. Podstawową zaletą takiego podejścia byłoby wykorzystanie praktyki przemysłowej i znajomości/rozumienia procesu.
Szczególnie istotne jest zagrożenie wynikające z możliwości przeniesienia się wybuchu, do którego dojdzie w aparacie procesowym, poprzez łączące go rurociągi/kanały na sąsiednie aparaty znajdujące się w ciągu technologicznym. Możliwe zniszczenia i konsekwencje finansowe wynikające z tego zjawiska mogą być zasadniczo większe niż zniszczenia wskutek wybuchu w pojedynczym aparacie. Trudniejsze do oceny są skutki wybuchu oraz skuteczne przeciwdziałanie.
Co prawda wiedza techniczna (oraz dostępne systemy izolacji [odcięcia] wybuchu) pozwalająca na eliminację zagrożenia przeniesienia się wybuchu jest dostatecznie duża, ale już sytuacja prawna [1] nie jest w tym zakresie jasna. Zapisy dwóch związanych z tym problemem paragrafów 4.2 i 12.2 w rozporządzeniu [1] nie są dostatecznie pomocne.
Zapis: §4.1. Aby zapobiec wybuchom i zapewnić ochronę przed ich skutkami, pracodawca powinien stosować, odpowiednie do rodzaju działalności, techniczne i organizacyjne środki ochronne. Określając środki ochronne, należy zapewnić realizację następujących celów:
• zapobieganie tworzeniu się atmosfery wybuchowej,
• zapobieganie wystąpieniu sfery wybuchowej,
• ograniczenie szkodliwego efektu wybuchu, w celu zapewnienia ochrony zdrowia i bezpieczeństwa osób pracujących.
Zapis: §4.2. Środki ochronne, o których jest mowa w ust. 1, pracodawca może łączyć lub uzupełniać środkami przeciwdziałającymi rozprzestrzenianiu się wybuchu. Sformułowanie „może łączyć lub uzupełniać” nie wymusza konieczności zastosowania środków przeciwdziałających rozprzestrzenianiu się wybuchu nawet, gdy jest to technicznie uzasadnione. Kto więc ma podjąć decyzję o zastosowaniu lub nie środków przeciwdziałających rozprzestrzenianiu się wybuchu? Przecież taka decyzja może nieść za sobą poważne konsekwencje prawne i finansowe.
Zapis: §12.1. Pracodawca powinien podjąć wszelkie niezbędne środki w celu zapewnienia, że miejsca pracy, urządzenia oraz elementy łączące dostępne osobom pracującym zostały zaprojektowane, wykonane, połączone i zainstalowane, a także są utrzymywane i działają w sposób minimalizujący zagrożenie wybuchem.
Zapis: §12.2. Środki, o których mowa w ust. 1, powinny zapobiegać wybuchowi, a w razie jego wystąpienia utrzymywać go pod kontrolą i minimalizować jego rozprzestrzenianie się w miejscu pracy lub w urządzeniach, a także minimalizować jego skutki dla osób pracujących.
Podobne problemy stwarza zapis „powinny”. Czy oznacza to konieczność minimalizacji rozprzestrzeniania się wybuchu w miejscu pracy lub w urządzeniach, czy raczej „dobrowolność”? No i kto ma za taką decyzję odpowiadać?
V. Alternatywne podejście do oceny ryzyka wybuchu
Jakie więc cechy powinna posiadać ocena ryzyka, by mogła się stać technicznie uzasadnionym narzędziem, które będzie brać pod uwagę podane wcześniej techniczne czynniki, uznane za istotne, a nie tylko potencjalne źródła zapłonu?
Możliwe skutki wybuchu (tabela 2) są uwzględniane i rozpatrywane podczas wyznaczania ryzyka R oraz na etapie tworzenia i analizy zidentyfikowanych scenariuszy awaryjnych. Scenariusze te są etapem końcowym oceny ryzyka wybuchu i wynikają ze znajomości i rozumienia procesu technologicznego oraz przyjętych zaleceń o charakterze technicznym, w tym zapewniających zabezpieczenia przed skutkami wybuchu. Scenariusze awaryjne powinny także brać pod uwagę nie tylko czynniki związane z wybuchem w pojedynczym aparacie, ale i zagrożenie przeniesienia się wybuchu w ciągu technologicznym z aparatu zagrożonego wybuchem na kolejne aparaty. Dotyczy to szczególnie ryzyka (konsekwencji) przeniesienia się wybuchu rurociągami łączącymi aparaty (rosnące ciśnienie i fala płomienia). Uwzględnienie tego zagrożenia jest bardzo istotne, a nawet kluczowe. Wymaga jednak odpowiedniego doświadczenia i praktyki w zabezpieczaniu przed skutkami wybuchu typowych węzłów procesowych.
W przypadku pracujących instalacji tworzone scenariusze awaryjne oceniają, w pierwszym etapie, spodziewane skutki wybuchu, biorąc pod uwagę aktualnie stosowane rozwiązania ochronne. Jeżeli zostaną one uznane za niewystarczające, to w kolejnym etapie proponuje się zastosowanie rozwiązań technicznych zmniejszających ryzyko (poprawiających bezpieczeństwo procesowe i wybuchowe) do akceptowalnego poziomu dla ludzi, otoczenia i środowiska.
Zastosowanie tego podejścia, już na etapie projektowania instalacji, ogranicza możliwość popełnienia (często kosztowych) błędów.
Proponowane alternatywne podejście do oceny ryzyka wybuchu wymagałoby, naszym zdaniem, stworzenia ogólnodostępnej i wiarygodnej bazy danych (o zasięgu europejskim) o zarejestrowanych wybuchach, ich przyczynach i konsekwencjach. Baza ta powinna być systematycznie uzupełniania. Do tego potrzeba współpracy odpowiednich służb technicznych krajów UE. To w konsekwencji (prawdopodobnie) wdrożenia nowej dyrektywy wymuszającej gromadzenie, opisywanie i udostępnianie pełnych informacji o tego typu zdarzeniach, przynajmniej w tych gałęziach przemysłu, w których doszło do zdarzenia wybuchowego.
Przekonanie społeczności UE do podjęcia wysiłków w celu utworzenia tego typu bazy nie będzie proste. To jest jasne, ale korzyści wynikające z tego dla zapewnienia bezpieczeństwa produkcji w przyszłości byłyby jednoznaczne: lepsza ocena możliwych zagrożeń prowadząca do większej „niezawodności” oceny ryzyka i tym samym lepsza ochrona zdrowia i życia ludzkiego, środowiska oraz miejsc pracy. No i nieocenione walory szkoleniowe wynikające z dostępu do tego typu bazy danych. Osoby oraz służby odpowiedzialne za bezpieczeństwo w zakładach przemysłowych mają prawo tego oczekiwać.
Wiarygodna baza danych pozwoliłaby na zmodyfikowanie podejścia do oceny ryzyka opierającego się na wyznaczeniu wartości ryzyka R. To podejście brałoby pod uwagę nie tylko potencjalne źródła zapłonu, ale i konstrukcję aparatu (smukłość), jego charakter pracy (ciągły/okresowy), objętość roboczą aparatu (minimalna objętość stwarzająca zagrożenie), charakter przepływu materiałów (ruch burzliwy/laminarny), własności fizyczne substancji sypkich (szczególnie minimalna energia zapłonu pyłu MEZ oraz przewodnictwo elektryczne).
Na przestrzeni dekady powstałaby wiarygodna statystyczna wiedza o zagrożeniach wybuchowych związanych z typowymi operacjami jednostkowymi. Ilustruje to tabela 5. Przyjęte dane dotyczące procentowego udziału zagrożenia wybuchem wywołanego określoną operacją jednostkową (aparatem) nie powstały na podstawie żadnej dostępnej bazy danych, a wynikają tylko z ogólnej wiedzy i doświadczenia. Tak więc mają one wyłącznie charakter informacyjny.
Tabela. 5. Procentowy udział typowych operacji jednostkowych jako potencjalne miejsce zagrożenia wybuchem
Z zestawienia tego wynika, że zdarzenia wybuchowe są, w pierwszym rzędzie, związane z procesem magazynowania i odpylaniem, a kolejno z mieleniem, transportem mechanicznym i suszeniem. Jeżeli tak, to podczas oceny ryzyka wybuchu na instalacji przemysłowej należałoby się skoncentrować, w podstawowym stopniu, na tego typu operacjach jednostkowych. I szczególnie w tych przypadkach brać pod uwagę możliwe zagrożenia wynikające nie tylko z potencjalnych źródeł zapłonu, ale także konstrukcji aparatu, jego działania, objętości roboczej, charakteru przepływu materiałów, własności fizycznych substancji sypkich.
Propozycję przyjęcia krytycznych wartości parametrów (czynników ryzyka) zestawiono w tabeli 6. Wyznaczone w niej wartości rozważanych czynników ryzyka mają co prawda charakter arbitralny, ale wynikają z wiedzy i doświadczenia autora. Należy jeszcze raz podkreślić, że przeprowadzenie tego typu oceny jest możliwe i realne tylko wtedy, gdy mamy dostateczną wiedzę o procesie i technologii. Podejście to zakłada, że w pierwszym etapie zostaną przeanalizowane możliwe źródła zapłonu a w kolejnym czynniki zawarte w tabeli 6.
Tabela 6. Czynniki ryzyka, które proponuje się brać pod uwagę na etapie oceny ryzyka wybuchu (wg kolejności podanej w tabeli). Dotyczy podstawowych operacji jednostkowych: magazynowania, odpylania, mielenia, transportu mechanicznego, suszenia.
** częste zatrzymania i uruchomienia
Przyjęte w tabeli 6 poziomy ważności poszczególnych czynników zagrożenia mają charakter arbitralny. Można się oczywiście pokusić o inny zestaw wartości liczbowych MEZ, S, Vrob czy DGW. Można by także przyporządkować wartości liczbowe do poszczególnych poziomów zagrożenia tak, jak to jest robione w standardowym podejściu do oceny ryzyka wybuchu. Prowadziłoby to jednak do powstania kolejnej „mechanicznej” procedury podejmowania decyzji.
Wydaje się jednak, że lepiej byłoby się oprzeć na doświadczeniu i wiedzy osoby wykonującej ocenę ryzyka wybuchu do podjęcia, w oparciu o dane zestawione w tabeli 6, decyzji o ochronie aparatu przed wybuchem (lub nie).
Można by również rozważyć przyjęcie zasady, że w przypadku gdy wartości MEZ < 20, S > 5, Vrob > 5, praca okresowa (**) oraz DGW < 60, to byłaby to wystarczająca podstawa do podjęcia jednoznacznej decyzji o konieczności zabezpieczenia węzła procesowego przed wybuchem (ochrona aparatu oraz zasypu i wysypu). VI. Bezpieczeństwo prowadzenia procesu a trening personelu Bezpieczeństwo procesu, i tym samym wynikające z tego ryzyko, zależy także w dużym stopniu od personelu, który go obsługuje, w tym również od znajomości oraz rozumienia procesu. Dlatego tak ważne jest utrzymywanie efektywnego programu szkoleniowego jako elementu zarządzania ryzykiem. Poprawne zadziałanie operatora w sytuacji zakłóceń pracy instalacji jest tak dobre, jaka jest częstość i efektywność dostarczanego treningu (rozumienie zagrożeń i proponowanych rozwiązań ograniczających te zagrożenia). Cały personel instalacji (zakładu), włączając w to kierownictwo, nadzór, utrzymanie ruchu, pracowników operacyjnych, pracowników utrzymujących porządek, powinien posiadać świadomość zalet wynikających z treningu dotyczącego zagrożeń wywołanych obecnością palnych i wybuchowych pyłów, gazów i par cieczy oraz mieszanin hybrydowych, współmierne z ich odpowiedzialnością. Ma to na celu zminimalizowanie zagrożeń wynikających z ich obowiązków zawodowych. Trening powinien, między innymi, dotyczyć identyfikacji rodzaju i zasięgu stref zagrożenia wybuchem oraz stosowania odpowiednich środków technicznych i organizacyjnych prowadzących do minimalizacji zagrożeń. Rozumienie ważności stref zagrożenia wybuchem oraz możliwych źródeł zapłonu jest czynnikiem podstawowym. Cel jest jasny: nabranie bezpiecznych nawyków w pracy. VII. Mieszaniny hybrydowe Zakres przedstawionych powyżej rozważań ograniczony jest tylko do pyłów. Uznano jednak, że istnienie mieszanin hybrydowych jest ważnym, a stosunkowo mało znanym i rozumianym zagadnieniem. W grę wchodzą mieszaniny palnych i wybuchowych gazów i/lub par cieczy organicznych oraz palnych i wybuchowych pyłów i włókien. W praktyce jest to mieszanina palnych i wybuchowych substancji w różnych stanach skupienia. Trudność w ocenie zagrożeń wynikająca z obecności mieszaniny hybrydowej wynika z faktu, że mieszanina ta może się zachowywać odmiennie od zachowania samych gazów/par, pyłów czy włókien [6]. Nie ma bowiem wzorów, które pozwoliłyby szacować, z dostateczną dokładnością, wartości podstawowych parametrów tego typu mieszanin związanych z zagrożeniem zapłonem i wybuchem, jak np. maksymalne ciśnienie wybuchu Pmax, stała wybuchowości Kst czy MEZ. Nie ma także w tym zakresie zbyt wielu badań naukowych i technicznych. To powoduje, że w praktyce nie ma możliwości opracowania ilościowego przewodnika postępowania. Wykorzystanie wentylacji Zastosowanie wentylacji, jako sposobu kontroli tego typu zagrożeń, powinno być ostrożnie przeanalizowane. Wentylacja mechaniczna może bowiem ograniczyć zagrożenie wynikające z obecności palnych gazów/par, ale może zwiększyć zagrożenie wynikające z obecności palnych pyłów. Może mieć ponadto różny wpływ na zachowanie się poszczególnych składników mieszaniny. Granice stężeń Mieszanina hybrydowa może tworzyć atmosferę wybuchową poza limitami stężeń wybuchowych poszczególnych składników mieszaniny. Uważa się, chyba że są znane dodatkowe dane, że mieszanina hybrydowa jest rozważana jako wybuchowa, gdy stężenie składnika typu gaz/para jest > od 25% jego dolnej granicy wybuchowości DGW lub gdy stężenie pyłu jest > od 25% jego DGW. O ile jednak pomiary stężenia gazu/par są dostatecznie precyzyjne, to nie można tego powiedzieć o pomiarze stężenia pyłów, ze względu na ich zmienny w czasie charakter.
Limity związane z energią/temperaturą
Uważa się, że w przypadku mieszaniny hybrydowej wartości parametrów takich jak minimalna energia zapłonu MEZ i temperatura samozapłonu gazu/par lub minimalna temperatura zapłonu chmury pyłu dla mieszaniny mogą być niższe od wartości każdego z jej składników. W praktyce gdy nie ma dostępnych informacji, to należy przyjąć te wartości parametrów, które są najniższe dla danego składnika mieszaniny.
Wymagania dla stref zagrożenia wybuchem
Rozważania powinny brać pod uwagę strefy wynikające z obecności poszczególnych składników mieszaniny (gazów/par oraz pyłów/włókien). Należy zestawiać pary indywidualnych gazów/par i pyłów/pyłów o tym samym poziomie klasyfikacji, tak by zidentyfikować najgorszą możliwą sytuację. Przykładowo, gdy dla danego składnika brana jest pod uwagę strefa 21 i strefa 2, to dla mieszaniny powinna być rozważana strefa 21 i strefa 1.
Systemy ochronne
Z powodów podanych powyżej liczba rozwiązań ochronnych, które posiadają deklarację zgodności (i certyfikat Atex) jako system zabezpieczenia przed wybuchem, wywołany obecnością mieszaniny hybrydowej, jest niewielka:
• niektóre systemy tłumienia i odcięcia wybuchu wykorzystujące butle HRD z proszkiem tłumiącym,
• systemy odcięcia wybuchu oparte o zasuwy szybkiego zadziałania oraz zawory przeciwwybuchowe Ventex.
Jak więc pracodawca ma sobie radzić, gdy rozporządzenie ministra gospodarki (Dz. U. Nr 138, poz. 931 z 8 lipca 2010 roku – Atex Users) wymaga spełnienia warunków rozporządzenia (tzw. minimalnych wymagań) w każdej sytuacji procesowej? Pytanie pozostaje otwarte.
Literatura
[1] Rozporządzenie Ministra Gospodarki z dnia 8 lipca 2010 r. w sprawie minimalnych wymagań, dotyczących bezpieczeństwa i higieny pracy, związanych z możliwością wystąpienia w miejscu pracy atmosfery wybuchowej (Dz. U. 2010 nr 138 poz. 931).
[2] The RASE Project „Explosive Atmosphere: Risk Assessment of Unit Operations and Equipment”, EU Project No: SMT4-CT97-2169., March 2000.
[3] Norma NFPA 652 (B.4.5, wydanie 2016).
[4] PN-EN 60070-10-1: 2015. Atmosfery wybuchowe. Klasyfikacja przestrzeni. Gazowe atmosfery wybuchowe.
[5] PN-EN 60079-10-2: 2015. Atmosfery wybuchowe. Klasyfikacja przestrzeni. Pyłowe atmosfery wybuchowe.
[6] PN-EN 60070-10-1:2015, Annex I (s. 101).
Dostawa systemów uziemiających dla nowo budowanego zakładu producenta chemii budowlanej
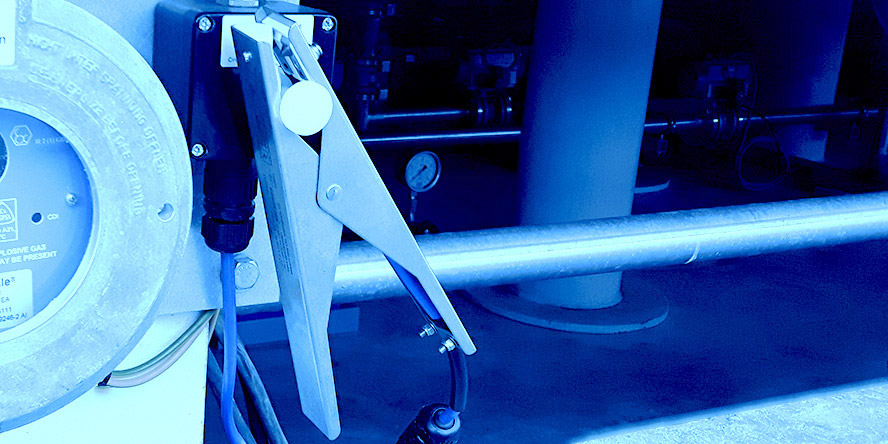
Zapobieganie wypadkom powstałym na skutek zapłonu atmosfery wybuchowej w następstwie wyładowania elektrostatycznego jest jednym z elementów polityki bezpieczeństwa wielu zakładów przemysłowych. Dla producenta chemii budowlanej świadomość ryzyka niesionego przez elektryczność statyczną w oczywisty sposób skutkowała inwestycją w systemy uziemiające.
W związku z tym dla nowo budowanego zakładu GRUPA WOLFF dostarczyła zaawansowany system Earth Rite RTR, którego zadaniem jest monitoring poprawności stanu uziemienia cystern drogowych podczas ich napełniania i opróżniania, oraz dwa systemy Earth Rite PLUS do uziemiana zbiorników IBC podczas procesów przelewania.
Dostarczone kontrolery uziemienia wykorzystywane będą na nowo wybudowanej instalacji komponowania rozcieńczalników. Urządzenia te przeznaczone będą zarówno do zabezpieczenia elektrostatycznego autocystern, jak i paletopojemników (DPPL) oraz standardowych beczek 200-litrowych. Kontrolery uziemienia zintegrowane będą z zaawansowanym systemem automatyki zarządzającym oraz wizualizującym całość pracy instalacji produkcyjnej, co pozwoli zarówno na bezpieczną pracę przy załadunku i rozładunku surowców, jak i na pełną kontrolę nad procesem oraz informowanie i zapobieganie potencjalnym zagrożeniom.
To nie pierwsza realizacja dla naszego Klienta. Dotychczas producent stosował w swoim zakładzie mniej zaawansowane rozwiązania, głównie przewody i zaciski uziemiające certyfikowane do pracy w strefach zagrożenia wybuchem.